MachinePix Weekly #2: Richard Whitney, set designer for OK GO
The story behind an OK Go music video, old-timey socks, and cocaine submarines.
This week, I interview Richard Whitney about building OK Go’s famous Rube Goldberg Machine for their This Too Shall Pass music video.
Submarines are back-to-back weekly Most Popular Posts. Last week’s was a US Navy nuclear submarine, this week’s is a narcotic-smuggling SPSS (self-propelled semi-submersible). The entire week’s breakdown is below the interview.
Oh, I also got an electric motorcycle. If anyone knows how to crack the firmware, please reach out ⚡️😈.
- Kane
Interview with Richard Whitney
We met while you were working at Particle, and I was surprised to learn you’d built some of the epic one-take music videos that OK Go is known for. What’s the story there?
In September 2009, I got pulled into this Rube Goldberg machine thing because a friend from grad school knew Damien [the OK Go lead singer], who was looking for mad-science-y types to make a video for the new album Of the Blue Colour of the Sky. The band wanted the video to have an organic, improvised feel rather than a precision machine.

RGMs are hard to make work once, and incredibly hard to make work many times in sync with music while looking improvised. They're inherently delicate and unstable because they're built on the careful management of potential energy. Triggers and effects can only consume so much before the machine would run out of energy and stop, so you make delicately balanced, easily triggered pieces and add reservoirs of energy like height and springs to keep it going.
How did OK Go pick the song for the video?
As I recall, some of us really liked White Knuckles for the video, but the band already had plans for it. This Too Shall Pass was the next choice, and it ended up being a great fit.

Where was the whole thing filmed?
The warehouse we used in LA was like a murder scene. Almost no light, graffiti all over the walls, major leaks in the ceiling, damage everywhere. We were allowed to use it because it was slated to be completely torn down. Somebody found out it had been one of the studios of Edendale, where silent films and early talkies were made in the early 1900s before Hollywood got hot. Charlie Chaplain movies were probably filmed there.

One of the most memorable things for me was walking through the space. We watched a lot of PythagoraSwitch and Der Lauf der Dinge for inspiration, and we were walking through the warehouse planning where parts could fit or work.

What was working with OK Go like?
They were super easy. They love arts and crafts and music and were really into it. Damien got really excited and had always wanted to be launched out of a catapult. It took a bit of convincing, but we talked him into doing a zipline instead. I was probably the big naysayer here—I didn’t want to kill a rockstar live on video!

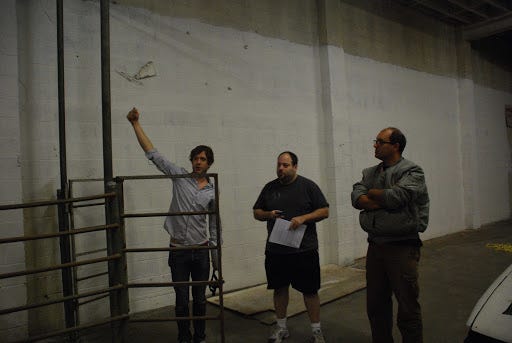
They’ve made several more videos and I’ve been invited to go work on some but I’ve always been stuck at work in San Francisco.
What is the craziest story you’re allowed to share from the OK Go experience?
Early in the planning I had really wanted to use a timing cable that ran behind the whole thing to work as a global trigger—one of the key asks by the band was that the actions would happen in time to certain musical cues. With any sort of machine that’s tricky—with something like this which was extremely hand-built and discontinuous, I thought it may be impossible to make it fit the timing. In the end it was brute force and hard work: people in charge of sections of the Machine got assigned timing and musical cues. I had built laser timing gates to test the repeatability of sections of the machine, but I actually don’t think people ended up using them! Everyone just fine-tuned their section of the machine.
The paint cannons at the end were also interesting; I had done a lot of work with pneumatic cannons before, but I was still pretty concerned shooting them at the band. If the pressure is off or there’s foreign material contamination, it turns into an actual cannon. The most stressful part for me was when I was out of town and receiving calls from the team asking me to clarify design intent and specs on these paint cannons that we were going to fire at the band.

The ball bearing race at the beginning was something I built. It’s really nice because I designed the timing to be tunable just by adjusting the incline. It worked great in testing and we were very happy, but there was enough humidity in the warehouse that the wood swelled and the ball bearings stopped fitting, and my poor friend spent hours sanding the tracks. He eventually gave up and bought smaller ball bearings, but was so frustrated that we only used one for the shoot instead of all three.


Funnily enough, I brought a lot of stuff to the set including dining room chairs, subwoofers, tools, but the only thing I got back was the plywood.
Especially for fans of the videos, what should we watch out for?
There are a couple of places where the band members will think it was a bad take and stop singing and look at the camera or their bandmates or the crew. When the bowling bowl goes down the spiral, you can see Tim flinch away for it—I can vouch for it being terrifying. That ball whipped around the track really fast and you’re inches from it.

Right before the finish, there’s a 55 gallon drum that rolls down and bounces—just after it leaves the screen, you can see the whole shot wobble because it hits the camera man but he’s such a pro that he keeps going and finishes the take.

It sounds like it was chaos. Were there any injuries?
Not that I heard about! But ironically State Farm sponsored it so we were joking we had insurance. Before they came onboard the band was paying for it out of pocket and we all worked for free because we were so excited about it.
What happened to the crew afterwards?
I had to go complete some other client work a couple of weeks before the big shoot. I thought I’d be back after a week, in time to finish up some effects and help on the shoot day. A tragedy of errors and three blizzards kept me in NYC for an entire month, so I was stuck in NYC during the final shoot.

There are so many people that worked way more than I did on this project, especially when they had to cover for my absence, and I am eternally grateful to everyone who worked on it.
They really made it happen. The video’s up to about 65 million views now and won several awards, and the credit really goes to those folks who pulled it together at the end. Syyn Labs was formed partly as a result of the video and we got a lot of requests to build Rube Goldberg installations for stunts and museums. The core group from Syyn Labs eventually went on to found Two-Bit Circus.
I saw that you went viral last year for one of your design studio’s products, the Alexaphone. Tell me about what inspired this and where that project is now!
It started as a joke. Christine and I thought “wouldn’t it be funny if you had a voice assistant in an old-timey candlestick phone?” so I built one intending it to be an April Fools video. I showed it to a couple of friends, who loved it and suggested that I should sell them. Initially I tried to source replica telephones to make a smallish production run, but only a few places make them and the quality is unbelievably terrible. All hand-built, no QA. Crazy things, like handsets stuffed with newspaper to make the parts fit and phones where all of the screws are different, and grinder marks everywhere.
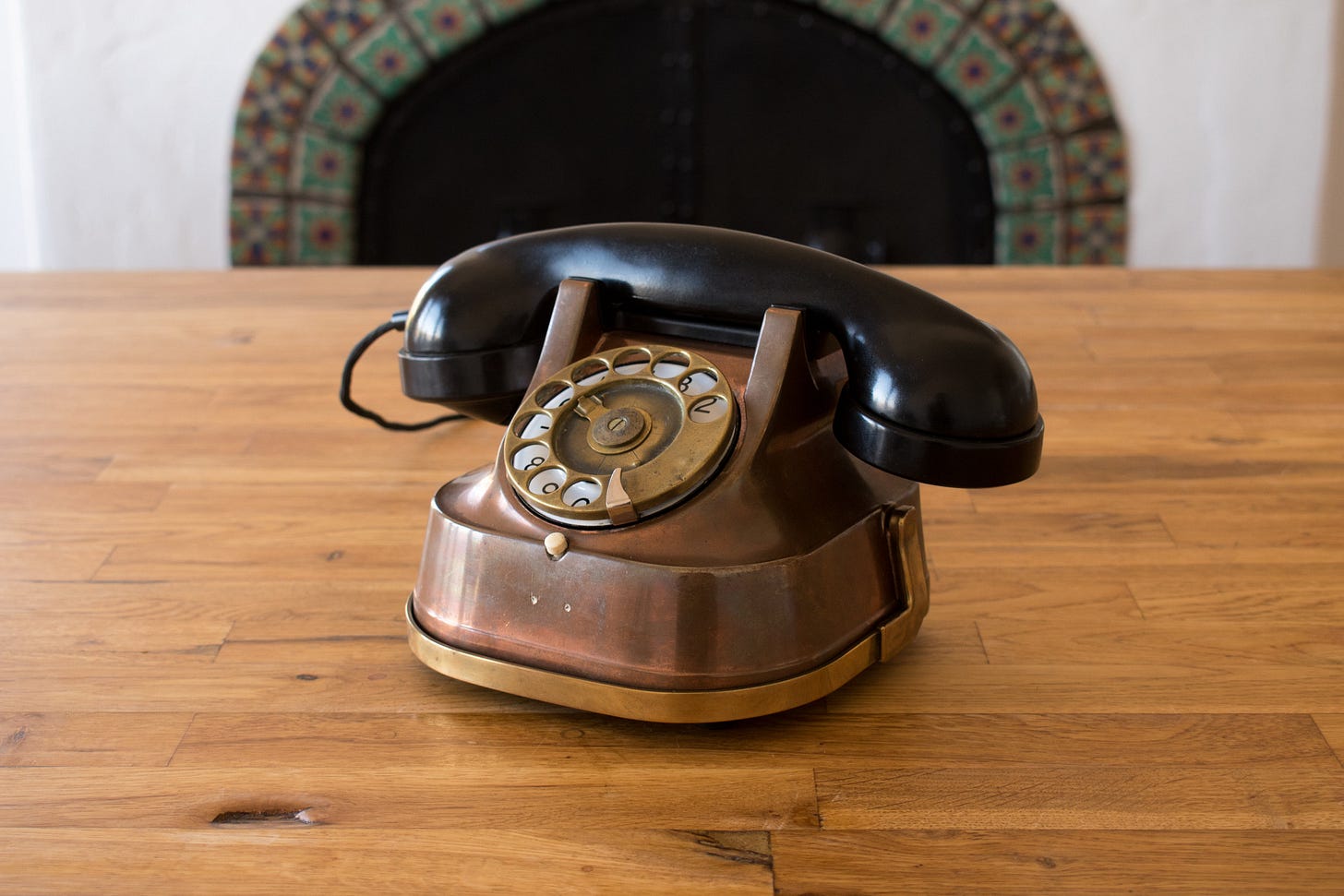
That sourcing issue was the main reason I ended up using the actual antiques—and it was so obviously right as soon as I switched. So much better, but every one takes a fair bit of labor to clean up and has unique challenges to integrating the electronics. I was willing to make 10-20 so I went way up the price curve and made them $1,500. We sold 10 in the first week, including all of the photographed ones on the first day.
Christine’s responsible for the viral success between her fantastic writing, working on the site, and her fantastic eye. Now I’ll sell one every few months, mostly from the original media coverage, and the process of making them singly is very pleasant because it’s fun, manual, detail oriented labor. One just sold to a famous country music star.
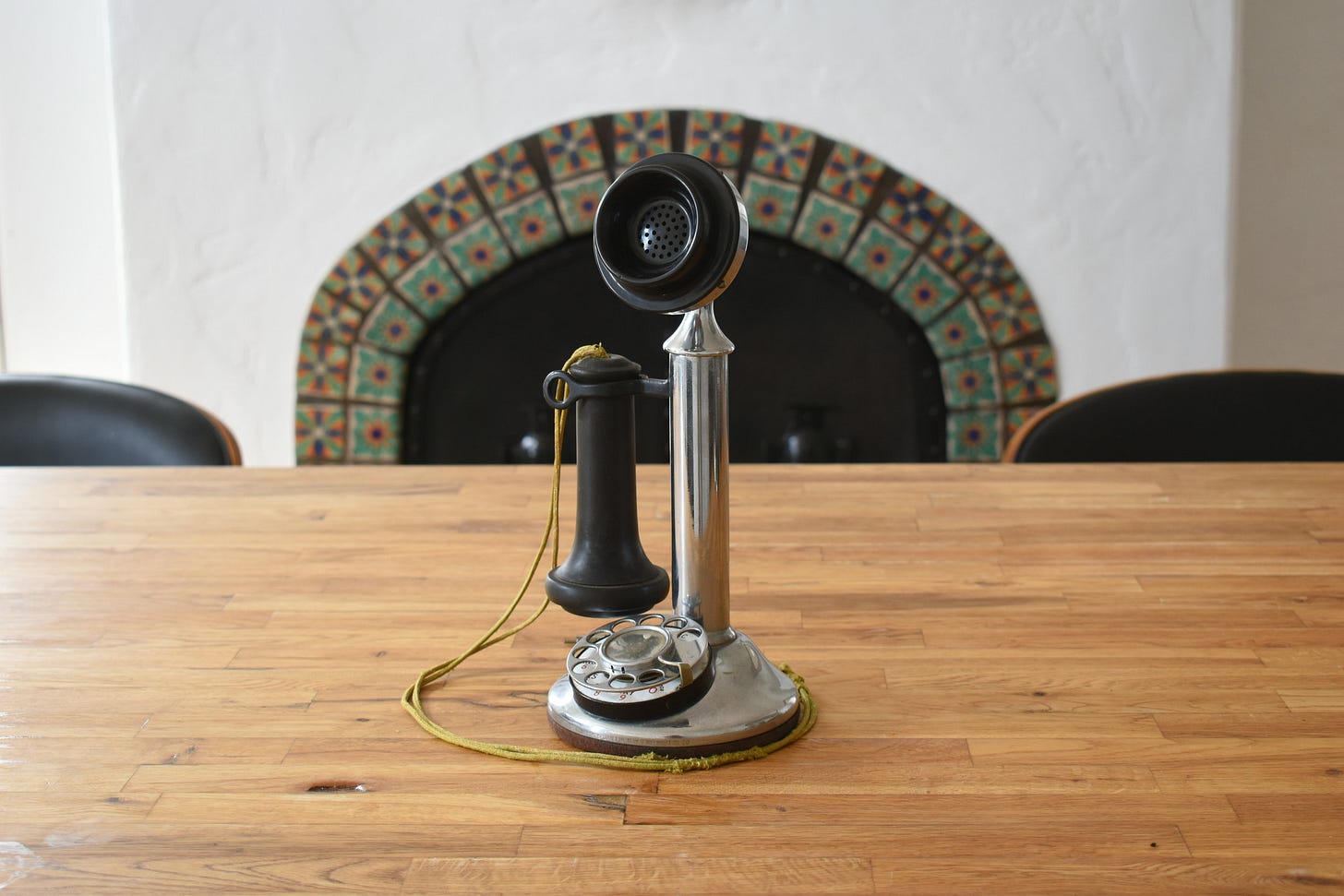
What’s special about these phones?
To the extent possible I tried to use the original switches and speakers to maintain the feel of the phone. They’re much heavier than you expect; there’s a sense of density that’s uncommon in new products. I actually physically defeat the microphones on the Alexa, and the remaining mic is wired through the original handset rest in the phone. The speaker is also the original speaker, so you get this great vintage sound.


There’s one Alexa button I need to make available for setup, but many phones don’t have an obvious place for it and I didn’t want to drill or modify the body. One of the tricks I’ve used is to install a tilt or mercury switch inside the base, so holding it upside-down puts it in setup mode.
What’s your favorite simple (or not so simple) tool that you think is under-appreciated?
I discovered you can buy cheap surgical loupes now. They are almost as good as having a dissection scope for electronics and a lot cheaper. RotoDrive Countersinks are these great little manual countersinks I use all the time for cleaning up parts.
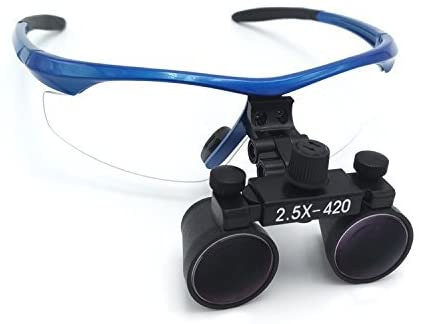
The Week in Review
July 25, 2020: Crew from Coast Guard Cutter Munro capture an illegal semi-submersible cargo ship carrying 8.5 tons of cocaine.
There’s an entire taxonomy of SPSS (self-propelled semi-submersible) and they’re pretty impressive. This particular SPSS was carrying a mind-boggling $192 million worth of cocaine.
Manufacturer: SPSS: Cartel craft-built; Coast Guard Cutter Munro: Huntington Ingalls Industries
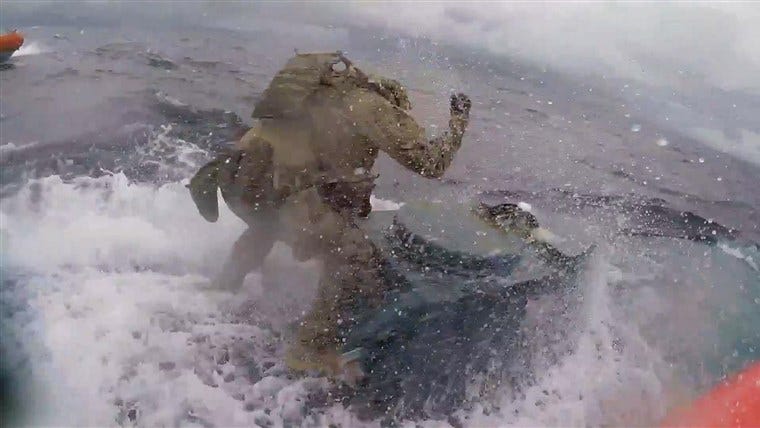
July 24, 2020: Gearhart circular sock knitting machine via The Odd Sockery.
While Gearhart is out of business, the great-grandson of founder Joseph Gearhart has generously digitized much of the company’s archives. You can still purchase socks made on these very satisfying machines operated by The Odd Sockery.
Manufacturer: The Gearhart Knitting Machine Company

July 23, 2020: Cutting trenches in cotton fields to install Smart Syphon irrigation by Islex.
Nothing of particular note here, just some cool earthmovers.
Manufacturer: Islex Australia

July 22, 2020: Submerged arc welding by Legion Piping Fabricators.
SAW is useful for long welds with thick material, like in structural or pressure vessels. The sand-looking stuff is a flux blanket, which generates a protective gas shield and can be used to add alloying elements as well.
Manufacturer: Legion Piping Fabricators

July 21, 2020: Firefighting RXR-MC80JD robots by CITIC Heavy Industries.
The Colossus got 15 minutes of fame for deploying during the Notre Dame Cathedral fire, but I’m curious why we don’t see more firefighting robots. Let me know if you know the answer. If you look closely at this video, you can see the RXR’s continuously spraying fluid on themselves—I’m guessing as a thermal shield.
Manufacturer: CITIC HIC Kaicheng Intelligence / Heavy Industries
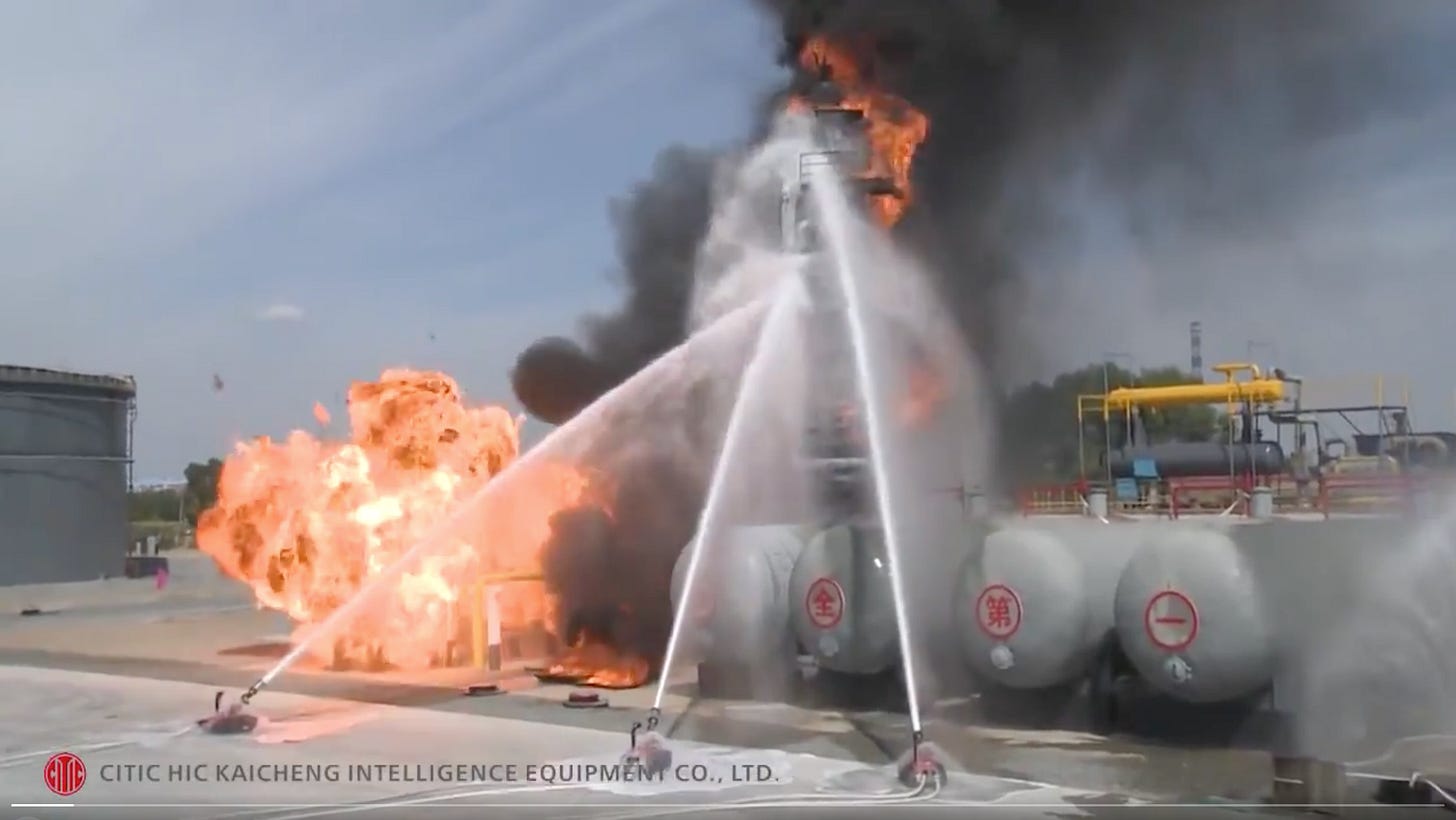
July 20, 2020: Testing the Ignition Overpressure and Sound Suppression at Kennedy Space Center's Launch Pad 39B. The IOP/SS water deluge system uses a half million gallons of water to cool and stabilize launches.
This pops up on the internet every once in a while as an “emergency fire extinguisher”, which is blatantly wrong. It’s used for cooling and sound suppression for the upcoming SLS (Space Launch System) launches, which are so violent that without the IOP/SS the sound and heat would destroy nearby infrastructure.
Manufacturer: NASA

Errata
Last week’s issue incorrectly linked the fabulously popular “Jizhou ware ceramics from Jiangxi, China.” to a video of an ambulance crash test. Oops.

If you enjoyed this newsletter, forward it to friends (or interesting enemies). I am always looking to connect with interesting people and learn about interesting machines—reach out!
- Kane