MachinePix Weekly #26: Frank Ippolito, founder of Thingergy, Inc.
Frank Ippolito talks about how he started off making toys and ended up making costumes, makeup, props, and more for major TV and movie productions. This week's top post was fake lettuce š„¬
This weekās interview features Frank Ippolito, the man behind Thingergy, Inc. Thingergy makes costumes, props, statues, special effects makeup, and all manner of things for movie, TV, and video game universes.
Check out more of their work at ThingergyInc.com, and Frankās personal projects at @frankippolito.

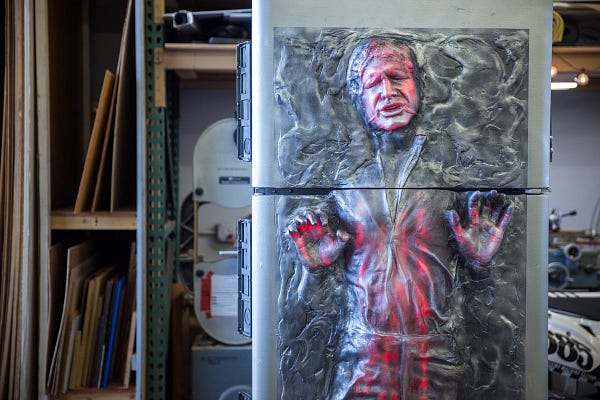
The most popular post this week was replica lettuce for restaurant displays. Known as shokuhin sampuru (é£åćµć³ćć«) this industry is centered in Gujo Hachiman, Japan.
Iām always looking for interesting people to interview, have anyone in mind?
āKane
Interview with Frank Ippolito
You started in toy mold making, what was your original goal?
Yea, one of my earlier jobs was working for MacFarlane Toys. I worked there for about two years on action figures, primarily making silicone molds for sculptures and accessories. I got really good at making molds of small intricate things, which paid off later. It was shortly after I quit college. I went to school for a short amount of time for Industrial Design; I realized I wasn't as good at drawing cars as the other students, I liked making monsters more. I left school and tried to figure out what the hell to do with my life.
This was ā96. ā98? Yea probably ā98, pre-most of the internet. There really weren't the communities you can find now on the internet. Now if you want to sculpt you can find communities, YouTube videos; back then, you had to organically meet people and get lucky. I had no idea what to do, and I had gotten a job offer from someone I knew from school and it was better than doing nothing. Toys are cool, but it was never my big passion. I always assumed it was a stepping stone.
How did you end up in prop and costume for Hollywood? What do I call it?
Itās hard to put a title on it, we kind of make all of it. That's why weāre called Thingergy, itās not just props, or costumes, or sculpturesāitās really anything we can think of. We just make things.
Well, Iāve always been a bit of a generalist, and I have a lot of mechanical intuition and enough art sense that I can get my hands into everything. I always wanted to work in the film industry because it was really cool, and it gives me the opportunity to work on all the different things. Iām not just stuck making toys, or hand props, or costumes.
I donāt know if there was ever a transition, it was me just constantly looking for a way to do whatever's fun.
Was there a moment where there was a breakthrough?
When I first moved to LA, within the first 6 months I worked on my first movie, Reign of Fire with Matthew McConaughey and Christian Bale. Because of my toy background, I got to mold all the maquettes for the dragonsāa maquetteās a kind of like a sample sculpture, instead of building a full size dragon, we built a small one first. When I say small, it still had a twelve foot wingspanāit was still huge. Because of my toy background, I was doing the molds and casting for doing that.
This whole industry is freelance, so you go from one show to another, one job to anotherāwithin that next year, I canāt remember dates, but I worked on Buffy the Vampire Slayer, and that was the first time I was on a real set and that was really cool. I was on the set of Buffy the Vampire Slayer!
I worked on another cool project: Chronicles of Riddick which shot up in Vancouver. I didnāt get to explore much, whenever weāre on set thereās more work than there is time. I guess the first āthis is a big dealā moment was working on Pirates of the Caribbean. I was down in the Caribbean standing on the deck of the Black Pearl surrounded by the cast. That was so awesome.
When I worked on Star Wars: The Force Awakens for Tippet Studio, run by the legendary Phil Tippett, we made the chess set. The studio we were working with was in Berkeley and I met Carl Bass a few times. He was a super nice guy.
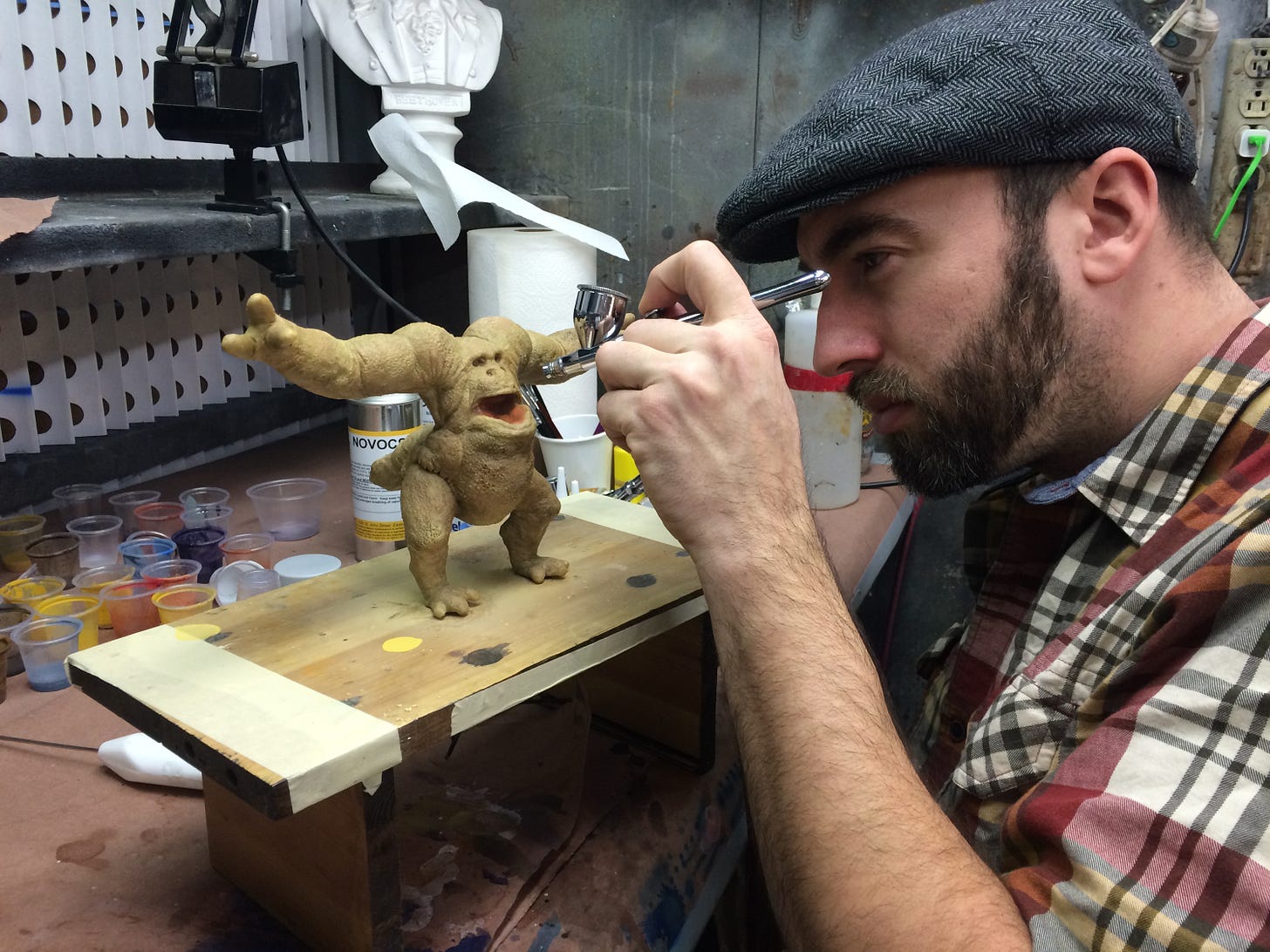
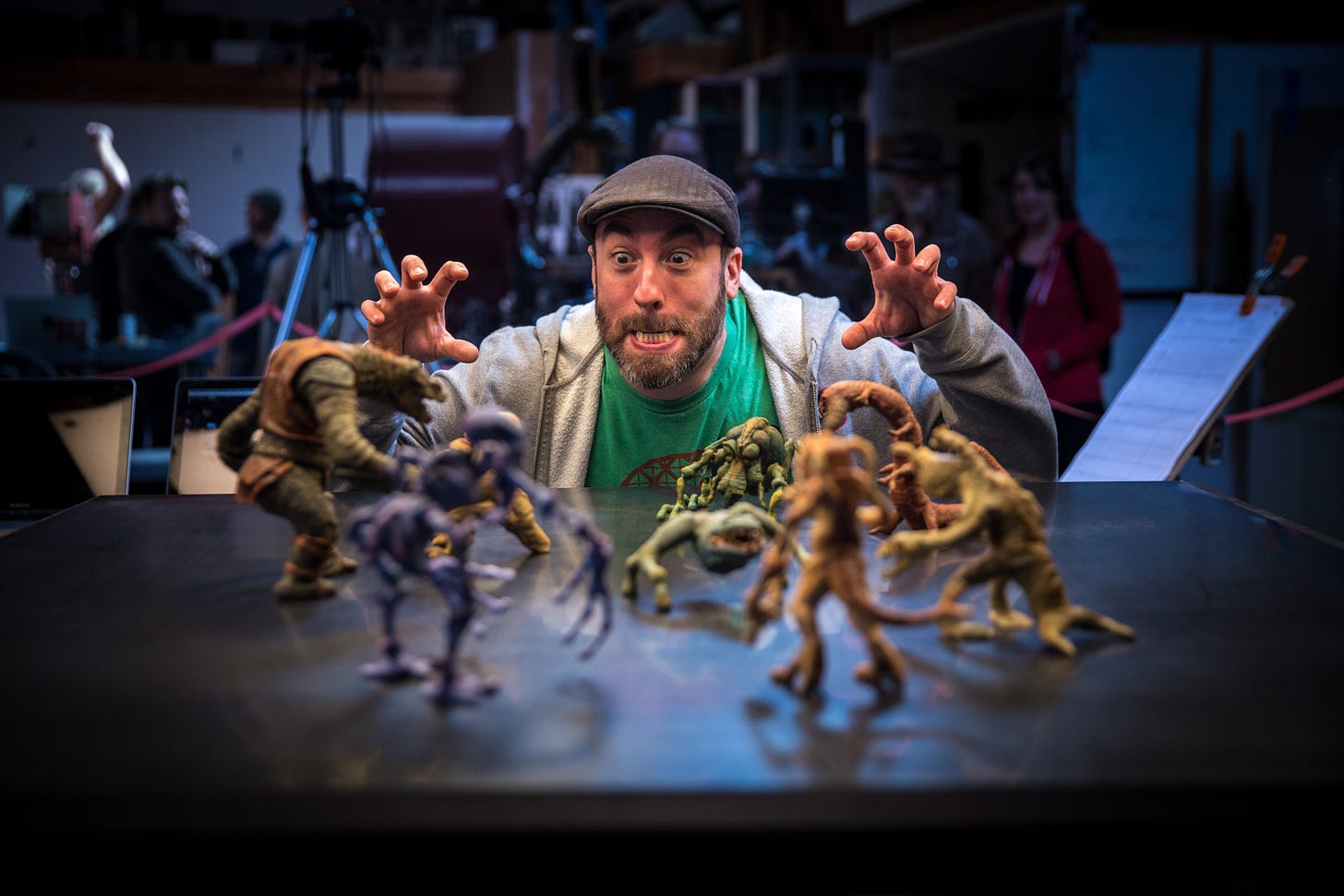
I know your work has appeared in AAA budget productions like Star Wars and West World; what was it like working for epic projects?
Fourteen year old me is like losing my shit. Forty-two year old businessman Frank is like āwhat the hell am I doingā. Just because these projects are top tier budget wise, every project has budget limitations and schedule limitations, and the nature of the film industry is everything changes every other day. Especially now with the pandemic, schedules change so fast. Itās chaos. Bigger budgets doesnāt mean more organized or efficient, itās all just chaos. Itās fun chaos though, you know? We kind of joke sometimes when weāre on these bigger shows that āthis is a $100M student film.ā No matter how big the budget, it always feels like a bunch of kids.
Thatās funny, from the outside these big studios feel like machines.
I talk to people in other industries, and they have the same challenges as us in the film industry.Ā Everything comes down to budget and schedule and vision.Ā And there has to be a happy middle somewhere in there.Ā And of course the human factor.
Whatās been your favorite project? Is it the really epic titles or something else?
You know, it changes all the time. Every single time I do a project, I think āhow could it get better than this?ā Working on Pirates, I never thought I'd top this. Then Star Wars. I donāt know if youāve dug deep enough, but I played one of the aliens in a recent Mandalorian. One of the Mon Calamaris. When Iām on set with Bryce Dallas Howard, I was thinking āhow do I get better than that?!ā but Iām sure something new will come up and itāll happen again.
Whatās your craziest story from your time?
Everything we do is a crazy request. Every job we do has not enough time, budgets are really tight, itās always something thatās never been done. I worked on a show, wonāt say which one it is, every time Iād turn in an estimate or budget Iād get a call from a producer saying āare you crazy, this is as much as a car!ā and Iād have to say āIām not selling you a car! Iām selling you something thatās never existed before.ā
As far as big hard things are challenging, we did a 14ā robot for Fox Sports of their football mascot, this big robot called Cletus. To build a 14ā tall statue to go into an office building, thereās a lot of logistics. How do you get it in and out, how do you keep it from falling over. I canāt remember off the top of my head but it was two, three thousand pounds of steel just in the base as ballast. To get it into the building, which only had double doors, it had to be a model kit with all these parts, it took a long time to assemble it. Thatās challenging.
The year after that, we did six 10ā tall statues for this game called Borderlands. Again, big statues like that need a lot of ballast, engineeringāone of them is pushing off on one foot and the whole statue is at an angle, and we had to figure out how to support that. Itās funny, at the time, I had someone working for me that had an engineering background, and literally every single challenge we had, this person kept saying how ridiculous it was and we didnāt have enough time, and I just kept saying we had to do it, we had to do it. This person from a professional engineering background just couldn't keep up with the pace. Some people just don't have it to roll with all the insanity. At the end of the day, all the math and figuring he was doing in his fancy software, we solved in a practical sense. Sometimes intuition and experience helps in a pinch.Ā
Any tips for how to watch for subtle prop and costume work like an expert?
You know what, the subtleties are best appreciated if you donāt notice anything at all. If you notice subtleties, weāre not doing our job right. The sign of good film work is if youāre not taken out of the moment. You can watch a film multiple times and watch for nuances in story, or beauty in art direction, or sound design and sound track, so thereās a lot of ways to watch a film, but if you donāt notice anything about the props, then weāve succeeded.
Fit and finish are the common mistakes. There are always things that will slip by because we donāt have enough time or money to make something perfect. When stuff leaves our ship we have a really high level of quality control: paint finishes, how things fit togetherāthat's what separates good shops from lesser good shops. There are a lot of hobbyists that make stuff they see in films. They may be good at modeling or designing in software, and a lot of times they can do it better than we did it for film! The challenge is we have insane schedulesāweeks, sometimes days, to do everything. So doing things well under pressure and living up the expectations of the fans with no time is the challenge.
Is there a canonical example of bad prop and costumes?
I wouldnāt put this in a major fuckup category, but in the first season of The Mandalorian, the biker scouts, and they have Baby Yoda in the back, all the fans exploded because they had their knee pads upside down. We built the costumes, but we didnāt dress the scout troopers. It could have been an oversight, it could have been the design saying āhey itās more comfortable this other way,ā and honestly it kind of is. But everyone noticed.
Any books youāre reading now or favorite books?
Oh yea, I am a crazy audiobook gobbler. I probably listen to two or three books a month. Right now, Iām listening to book eight of Expeditionary Force, and right before that I finished book four of the Bobiverse. Thereās a series called We Are Legion (We are Bob) by Dennis Taylor. Thatās one of my favorite book series hands down. Expeditionary Force is equally awesome.
Any side projects youāre working on right now?
I have about a million of those, the big one on my plate right now, Iām restoring a 1995 Ducati Monster 900. I stripped it down to nothing, we rebuilt the engine, powder coated the frame, itās going to be like a brand new bike when itās all done. Thereās about 6 to 8 months left to finish it.Ā I had a lot of time during lockdown. Nothing sounds like an open clutch Ducati. It constantly sounds like itās going to rattle itself apart. When you shift it sounds like you hit it with a hammer. Iāve spent way too much money replacing every steel bolt with titanium.
Whatās your favorite simple (or not so simple) tool or hack that you think is under-appreciated?
Iām very much a right tool for the right job kind of guy, and we do a lot of different things. I donāt particularly love sending stuff out to get done, so we have CNCs and 3D printers here. We try to do everything we can under our roof for quality control and design iterations really fast.
The Week in Review
You kind of have to throw out your intuition of how fluids work when you go to space. This is a cute example, but more terrifying ones include treating an astronautās blood clot on the ISS.
Props to whoever realized concrete pulverizers look like dinosaurs and followed through. I believe this is a Nye 40CP49U.
I never knew there were braided mozz products!
Postscript
Iām just a manufacturing dilettante, but I have the privilege of working with some real bad-ass professionals, including those at Instrumental. They are hosting their annual Manufacturing Optimization Summit remotely this year, and if your job is involves getting your hands dirty with design or supply chain, I encourage you to check it out.
If you enjoyed this newsletter, forward it to friends (or interesting enemies). I am always looking to connect with interesting people and learn about interesting machinesāreach out!
āKane