MachinePix Weekly #30: Dr. Steve Gass, inventor of SawStop
Dr. Gass talks about creating a best-in-class power tool, stressful trade shows, and the famous hot dog demo ššŖ. This week's most popular post was a scrap rebar straightening machine.
This weekās interview features Dr. Steven Gass, the inventor of the SawStopāconsidered one of the best table saws (we love the one in our office!).
SawStop has a unique safety feature that automatically brakes the blade if a finger touches it. Table saws are one of the most dangerous pieces of woodworking equipment, averaging ~150 injuries a day with ~8 of them being amputations š³
The most popular post this week was a rebar straightening machine of unidentified make. Sharp readers commented that this is almost certainly for scrap rebar, since they would not want to use rebar that had been bent multiple times and fatigued.
Iām always looking for interesting people to interview, have anyone in mind?
āKane
Interview with Dr. Steve Gass
You have both a physics PhD and law degreeāhow did you end up in the world of power tools?
Well you know, I grew up doing woodworking. My first memories are in my dadās shop, and Iāve always loved building things. That can be anything from furniture to houses to software to RC airplanesāit almost doesnāt matter what it is. I just like figuring out stuff and building. I knew in sixth grade I would get my PhD in physics. That was perfect for me. I was in graduate school, and I loved academiaāI would have loved to stay.
But what it turned out, what I realized, is as you advance in your career in academia, you end up spending your entire career searching for funds, grants. That to me sounded just dreadful. I figured if I was going to do that, I should just be a lawyer.Ā (Editorās note: Seamus, āFather of the Xboxā was also a physics Ph.D; and Jeff, fmr. Director of Robotics for Google, got an early start with RC aircraft).
At the time I started SawStop I was actually a partner at a patent law firm in Portland. My partners that I rounded up to help with SawStop were actually from my law firm. We started as four attorneys! It was an interesting thing from a patent perspective, there was not a lot that had been done in this area, and that opened a field for us to open up and play with. That was key because when we went out to raise money, we were able to work with companies that usually run roughshod over individual inventors.
What was the inspiration for SawStop?
I was out in my shop one day, and I looked over at my table saw, and the idea kind of came to me. I wondered if one could stop the blade fast enough if you ran your hand into it to prevent serious injury. I didnāt really have a compelling reason why that question came upāit just happened. Serendipity!
Once the question came up, I thought, well, how fast would I have to stop the blade? If youāre feeding material fast, that may be about a foot a second. Itās common for people to just feed their fingers through fast and lose them before even flinching. I figured I couldn't have more than a ā ā cut when it was all said and done. At a foot a second, 10ms gives me about a ā ā deep cut.
I also figured I needed on the order of 1000 lbs of force at the radius of the blade to stop itāIām a physicist by training, so I think in orders of magnitudeāwhich seemed doable! It wasnāt 10,000 lbs or anything. So that's how it started.
What about other saws? Did you consider those opportunities?
I had an intuition that the table saw was the most dangerous, but after reading up theyāre about 10x more dangerous than the other saws! Thereās a variety of reasonsāpart of it is that it just runs very fast. My sense was it was just very dangerous, and I knew people that had lost fingers. My first accident in a shop was on a jointer when I was about four years old, so I started early. Nonetheless the table saw seemed like the logical choice.
After the table saw, I thought I could do it on a lot of different tools. The key to the technology was the actuator that triggered the brake. Itās hard to get something to move or stop in under 10ms. The blade is spinning at 4000 RPM, that brake has to trigger on the order of a millisecond. The force required to do that is incredible because the T (time) component is so small.

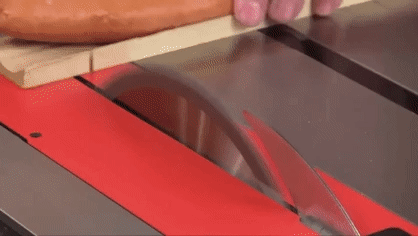
I started puttering around on how to stop things quickly. The simplest would have been a solenoid, but that would have been too slow and weak. I had come from RC airplanesāso I used the nose landing gear torsion spring from an RC airplane for an early experiment, that spring provided the force and I held it back with a fuse wire, a maybe 10 thou diameter fuse wire. I set up some capacitors to discharge through the wire and melt it in a few milliseconds, and I was able to generate maybe 20 lbs of force against a blade. This concept ended up being very similar to what we did in the production table saw.
When did you decide on using the famous hotdog demo? Was there a predecessor?
What was the first thing? It was probably a stationary blade with me just touching it with my finger. Once we started spinning the blade, I wasnāt too eager to do that test with my finger, so we just thought āwhat do we have thatās sort of finger like with similar electrical propertiesāāhot dogs are similar, and I had one in the fridge, so I grabbed one and ran it into the blade. Sure enough, it worked.
There was a point where we had to know a hotdog was a good surrogate for a finger. You can imagine, we could do this demo at trade shows with a hot dog, but thereās always a smart-ass that says they don't care about hot dogs, and wanted to see it with a finger. So before the first trade show I had to test it with my actual finger. Thankfully it worked!
That must have been a stressful moment.
Yea, the braking action is very powerful. When the brake goes off itās a big reactionāa sudden bang, very dramatic. Like popping a balloon with your face. You know it wonāt really hurt, but thereās a certain reluctance. It was not an easy thing to do, but you knew that's the question youād get during demos so you had to have an answer.
Thatās funny because I come from a background in wireless networking, and we use potatoes as a surrogate for human bodies when studying signal absorption.
Hah. Whatās interesting with the hot dog, you actually have to be holding the hot dog for it to work. The hot dog is an extension of your body. [The saw is] detecting the capacitance of the human body which is 50-100 picofarads. If you put a hot dog on a sled and push it in, itāll just cut through the hot dog. We had dealers do this in front of customers and call us in a panic on why our system didn't work. Itās because they weren't holding the hot dog.
In the early 2000s you tried to license the technology out to a few well known tool makers like Craftsman and Black & Decker. What was that like?
Well, the one word that comes to mind is āfrustratingā. It was sort of futile. If you ask me what I regret or what I'd do differently looking back at the time weāve been doing SawStop, the one significant thing I would change is all the time we wasted trying to license it. We should have started building our own saw from the beginning. I remember being on the phone with four different lawyers when speaking to Bosch, and we went back and calculated the cost of the callāit came out to about a dollar a second.
The fundamental question came down to economics. Almost a societal economic structure question. The CPSC says table saws result in about $4B in damage annually. The market for table saws is about $200-400M. This is a product that does almost 10x in damage as the market size. There's a disconnectāthese costs are borne by individuals, the medical system, workers compāand not paid by the power tools company. Because of that, thereās not that much incentive to improve the safety of these tools. Societally if there was an opportunity to spend $5 to save $10, weād want to do that. But in this chain there's a break in people that can make those changes and people that are affected, so itās not done.
This goes back to why the power tool companies are interested in itāthey were interested in it, but it was hard for them to figure out how to make more money.
You ended up striking out on your own with SawStopāwhat were the wildest stories you can share from that time?
Luckily I canāt say we had that many wild stories! At one point, when we first started making the saws, we had an overmold on the arbor shaftāand we were having trouble with this material degrading over time. We had a disagreement with the manufacturerāwe wanted a tighter press fit, because we thought the issue was coming from a fretting motion. One of the manufacturerās engineers wanted it to be looser. We went back and forth and got the OK on our design, and received a couple containers of saws. Lo and behold, they started failing. We took them apart, and it turns out they had been made the overmold looser even though they told us it would be tighter. It was a huge pain in the ass. To their credit, they made good on itābut it was a huge hassle, and one of those things we just didnāt know we had to stay on top of. We had no idea we needed QC inspectors on the lineāNone of us had formally designed a product of any kind before.
Early on, our first demos at trade shows, we had a prototypeābut it was a rough prototype. When the saw blade retracted, the arbor block that held the blade up was held up with rubber bands. The prototype brake cartridge on that one, we used a 180V capacitor to burn the fuse wire to release the brake. The fuse wire went around this little clip, and it turned out occasionally the clip would contact the capacitor leads. When you went to grab the cartridge to change it, the capacitor would discharge into your hand, and youād have to try to maintain a smile while holding an electric fence. There were a lot of small things like that.
We had to do a live demo at the CPSC on CNN in front of the head of the CPSC. This was a huge deal for us. If it hadnāt worked, it would have been disastrous. We were there with this same prototype. Now we have self tests and everything and wonāt let you use it unless everythingās functional. Back then, we didnāt have any of those in the prototype and you had to cross your fingers.
Over the years, weāve had really few demo failures. There was one really amusing one in Germany. The audience didnāt speak much English and I didn't speak any German, so we were trying to get these German woodworkers to come see the demo. The one guy we dragged over, he didnāt speak English so he didnāt have any idea what we were trying to show him. So we get the hot dog out, and he gets a confused look. We try to mime at him to watch carefully. My partner David pushes the hot dog through the saw and it cuts right through. The woodworker looked at us like we were insane and we couldn't explain, so we just smiled. Oh man the look he gave us. Brake cartridges are designed to be used once, but those days, we were rebuilding the prototype brake cartridge at night in the hotel rooms for the demo. These SCRs we used, eventually they went bad after too many rebuilds. That night in the hotel we had to desperately figure out how to ensure that it would work. That was the first time weād seen that particular failure. Fortunately we figured out a way to test for it.
Whatās the best advice you have for people that are tinkering and exploring their own ideas?
I would tell people itās an uphill battle, always. You have to go into it with eyes wide open. We thought we really understood what we were doing and it was still hit or miss. There were a lot of times when something could have gone differently and SawStop wouldn't be around.
Are you working on any side projects these days?
Iāve got a new mitre gauge Iām working on here thatās going to be really coolāit wonāt be out for a while so I canāt say terribly much about it right now.
On the homefront, I have a TV lift so I could retract the TV into the floor of my shop. I used a cable winch to move it up and down, but it doesnāt make a very pleasant sound. The winch clunks a lot. So I got a ball screw and a stepper motor and Iām in the process of writing the acceleration profile to move this whole thing on a ball screw instead of a cable.
I have another thing for COVID, and I wonāt wear this on my head very long (Editorās note: I forgot to take a screenshot), but imagine I was blowing filtered air into this and you could see and hear people better, a low cost PAPR (Powered Air Purifying Respirator). I havenāt figured out what to do when the battery runs out. On the professional ones, people wearing them are trained on them know how to deal with the battery. On a low cost one, imagine the battery dies and you pass outāthat's a bad scenario.
Any favorite books or books youāre reading right now?
Actually I made a list for this! The one Iām reading right now is Brandon Sanderson's Stormlight Archive. I mostly read sci fi. My favorite is Patrick Rothfussās The Name of the Wind. Orson Scott Card, his famous one is Ender's Game, but I actually like Worthing Saga much more. Itās less well known, but I found it a really compelling book.
Whatās your favorite simple (or not so simple) tool or hack that you think is under-appreciated?
I did come up with my favorite recent one: tap sockets! At home, if youāre running taps in a drill, theyāre hardened and slip against the chuck sometimes. They make these things that are like a socket plug, you can get a set for $20 on Amazon, and you put it into your impact driverāoh my god itās SO much better. I got these six months ago and Iām like where have you been my whole life.
I could go on for a long time, I love tools. Iām lucky because I get the Festool employee tool discount and the Festool cordless impact drill, for drilling concrete, itās AWESOME. For putting up shelves, to go along with it, the drilling dust nozzle, the vacuum pulls dust straight out of the drill hole. Itās so well thought out.
The Week in Review
Etymologically, a āscreedā like a tirade was a long list of complaints or talking points, and a āscreedā like the one we see here is a long piece of material for levelingāboth originating from āscreedā as a variant of āshredā to mean a piece or strip of something removed. English is weird.
Retrieval time is 13 seconds! Detailed specs for your nerds.
My favorite reaction to this was a follower who had physically used this bridge multiple times without realizing that it rolled.
See the full time lapse here. If youāve ever wondered my people who design ships are called Naval Architects (versus say, naval engineers), this is a good indication as to why.
Postscript
My colleague Avidan is MCāing the Manufacturing Optimization Summit next week! If your job is involves getting your hands dirty with design or supply chain, I encourage you to check it out.
If you enjoyed this newsletter, forward it to friends (or interesting enemies). I am always looking to connect with interesting people and learn about interesting machinesāreach out.
āKane