MachinePix Weekly #4: Chrissy Meyer, first engineering program manager on the Apple Watch
Chrissy Meyer's stories from shipping the Apple Watch and Square Reader. Also, the Department of Wildlife that brought you fish airplanes has goat helicopters đđ
This week I sit down with my friend and co-worker Chrissy Meyer and talk about what it was like to ship millions of products as the Engineering Project Manager on Apple iPod, Apple Watch, and Square Readerâand how she got the nickname âLittle Princessâ from Foxconn leaders (hint: the Princess gets what the Princess asks for).
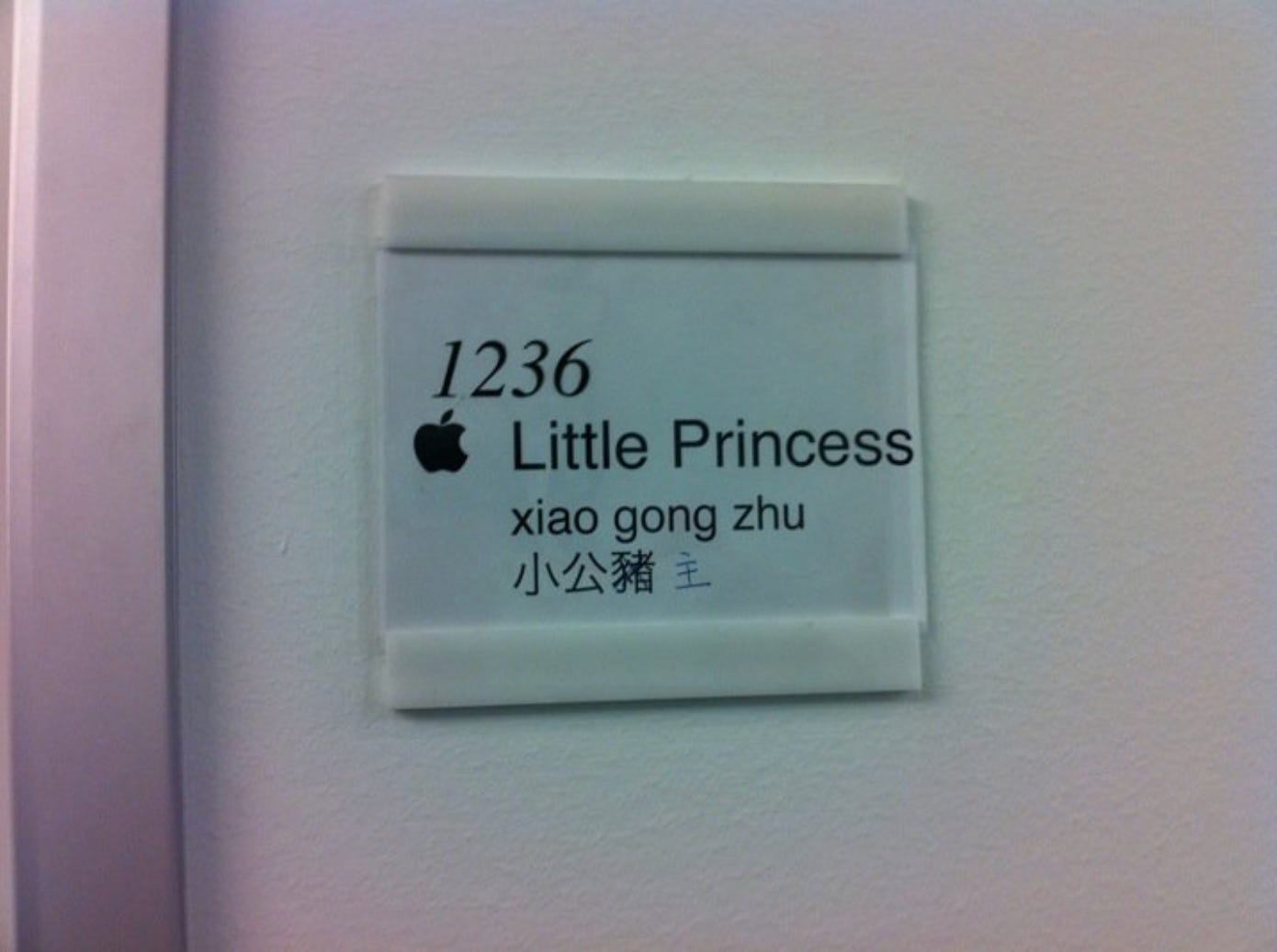
The most popular post last week was a wild 19th century safe. As always, the entire weekâs breakdown is below the interview.
Iâm always looking for interesting people to interview, have anyone in mind?
- Kane
Interview with Chrissy Meyer
I know you started in steel in and big diesel enginesâhow did you end up working on silicon valleyâs most successful consumer HW?
My first serious engineering job was at a steel processing plant in the backwoods of Kentucky, hours from any real city. I was hired to do controller programming on steel pickling lineâthe process of sending steel rolls through really concentrated hydrochloric acid bath to clean it. I was the only female in the entire plant with two to three hundred men. I was also by far the smallest person in the facility, so any time a machine broke down and someone had to climb into the grease filled pits to fix it, it was almost always me.
After I finished my bachelorâs degree in EE, I moved to Silicon Valley for grad school. To be honest with you, I pretty much just fell into an internship at Apple. Itâs funny how people talk about the value of networks out here, and I had zero network in California. Iâd been here for a month of two and went to a campus recruiting session for Apple because they had free pizza and I figured itâd be my dinner. Next thing I knew, they were calling me to interview.
I swear to you, I show up to the interview in a business suit off the clearance rack because I was coming from Kentucky and thatâs what you do. I had no idea how things worked in the Valley. My interviewer, who later became my manager, he was wearing some ripped jeans and flip flops. The first thing he said to me was âwow, youâre really over dressedâ. Thatâs how I ended up on the iPod team. The ironic part of it all is working as an EPM at Apple I spent so much time deep deep in the supply chain in Chinaânot that different than the factory in backwoods of Kentucky.
What exactly is an âEngineering Program Manager?â
Every company treats EPMs a little differently - sometimes theyâre called technical project managers. Even within big companies like Apple different teams treat the role very differently. You do whatever it takes on the product, process, or organizational side to ship a product.Â
In the world Iâm coming from, on any given day Iâd be constantly context switching between engineers in the lab debugging silicon to negotiating with suppliers on manufacturing issues to proposing new products to management. I loved how varied the role was. It gave me such an adrenaline rush.
What are misconceptions about building and shipping hardware that most people have? What donât people appreciate about hardware?
The thing I think people donât appreciate enough is the difference between having a functional prototype and a shippable product. The gap is huge. Just because something works doesnât mean you can make thousands, definitely not millions, and doesnât mean itâll work in all conceivable situations. There are zero take-backs in hardware. I donât want to bash software engineering friends, but we donât have the luxury of hitting a rollback button. Once itâs out there, you canât make changes. You have to be very very very sure what youâre sending out works. Especially on the consumer side: the industry term is âfield failuresâ and âwarranty returnsâ which can cause safety issues and PR nightmares. It can sink a startup.

The gap is timing, testing, and iteration. Assembly processes are their own engineering challenges and have to be repeatable and quality has to be consistent. Does it work in freezing temperatures? What if you leave it on the dash of a hot car?
It doesnât matter where youâre manufacturing, you canât just give a manufacturer a design spec and expect them to deliver. Any time you draft a design spec, you donât know what you donât know - manufacturing in volume has millions of edge cases. Manufacturers will sweep these under the rug unless youâre on top of it - theyâre trying to minimize time and cost.
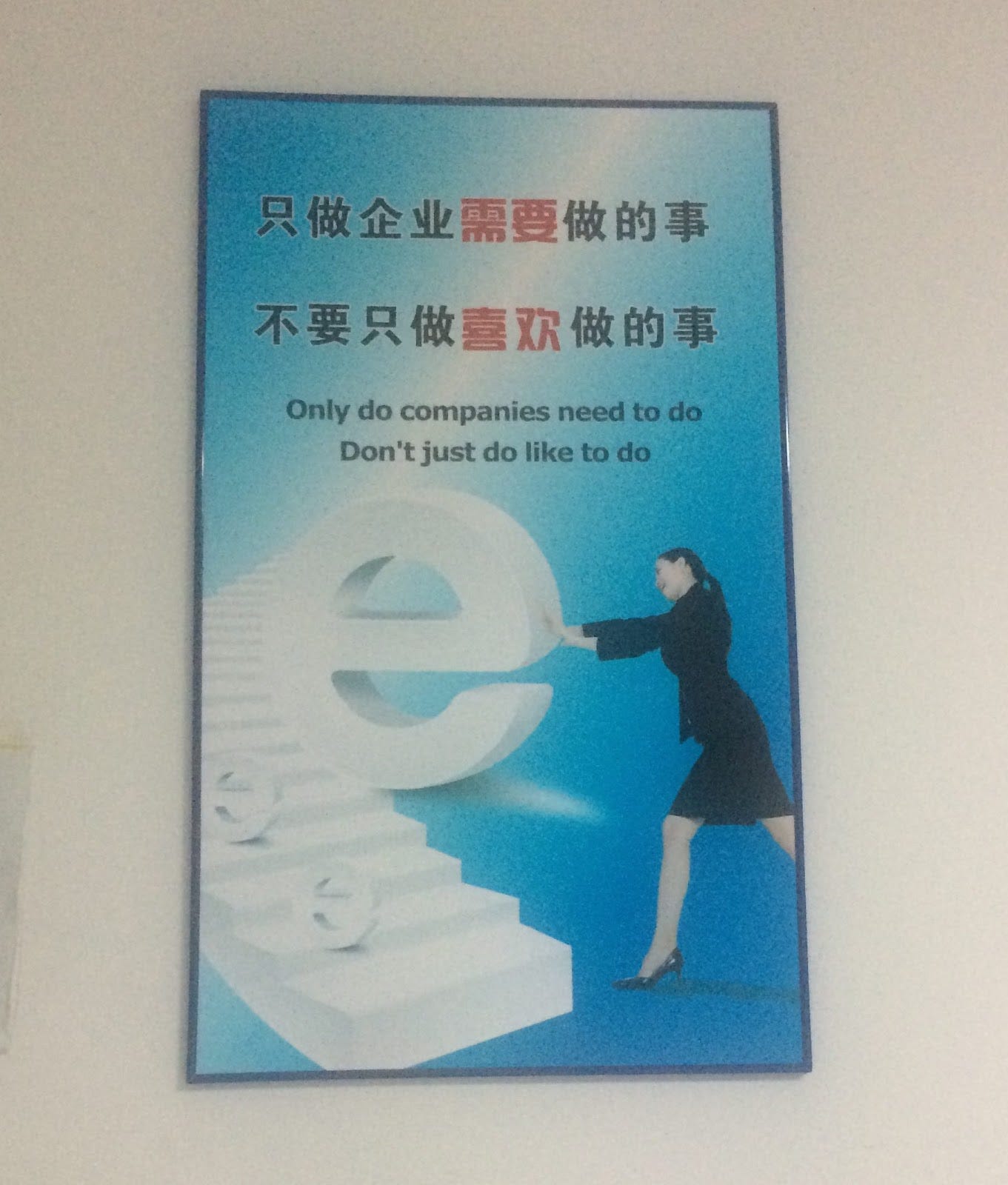
What are the funny stories youâre allowed to share from your time in manufacturing?
I had been working with the same factory for a couple of years, and had built pretty solid relationships with the engineers and managersâor so Iâd thought. Until during one night out (when we had consumed a few too many drinks), I came to realize that they had given Chinese nicknames to a handful of the key people on our team. This gave them a chance to talk about us in Chineseâright in front of our facesâwithout us realizing. I begged and pleaded to know what my nickname was. At first, no one would tell me. Finally, a few beers later, someone caved and told me that my nickname was ć°ć Źäž»Â (xiÇo gĆngzhÇ). Which directly translates to âLittle Princess.â The nickname stuck. By the time I got back to the US, practically everyone in the entire iPod division was calling me ć°ć Źäž» (xiÇo gĆngzhÇ). They even made me an office nameplate with the title. Mandarin is a tonal language, and most native English speakers have a difficult time getting the pronunciation right. So anytime an English speaker says it, the last syllable comes out as âzhĆ«â instead of âzhÇâ. Although it sounds similar, instead of translating to âLittle Princessâ, it translates to âLittle Pig.â
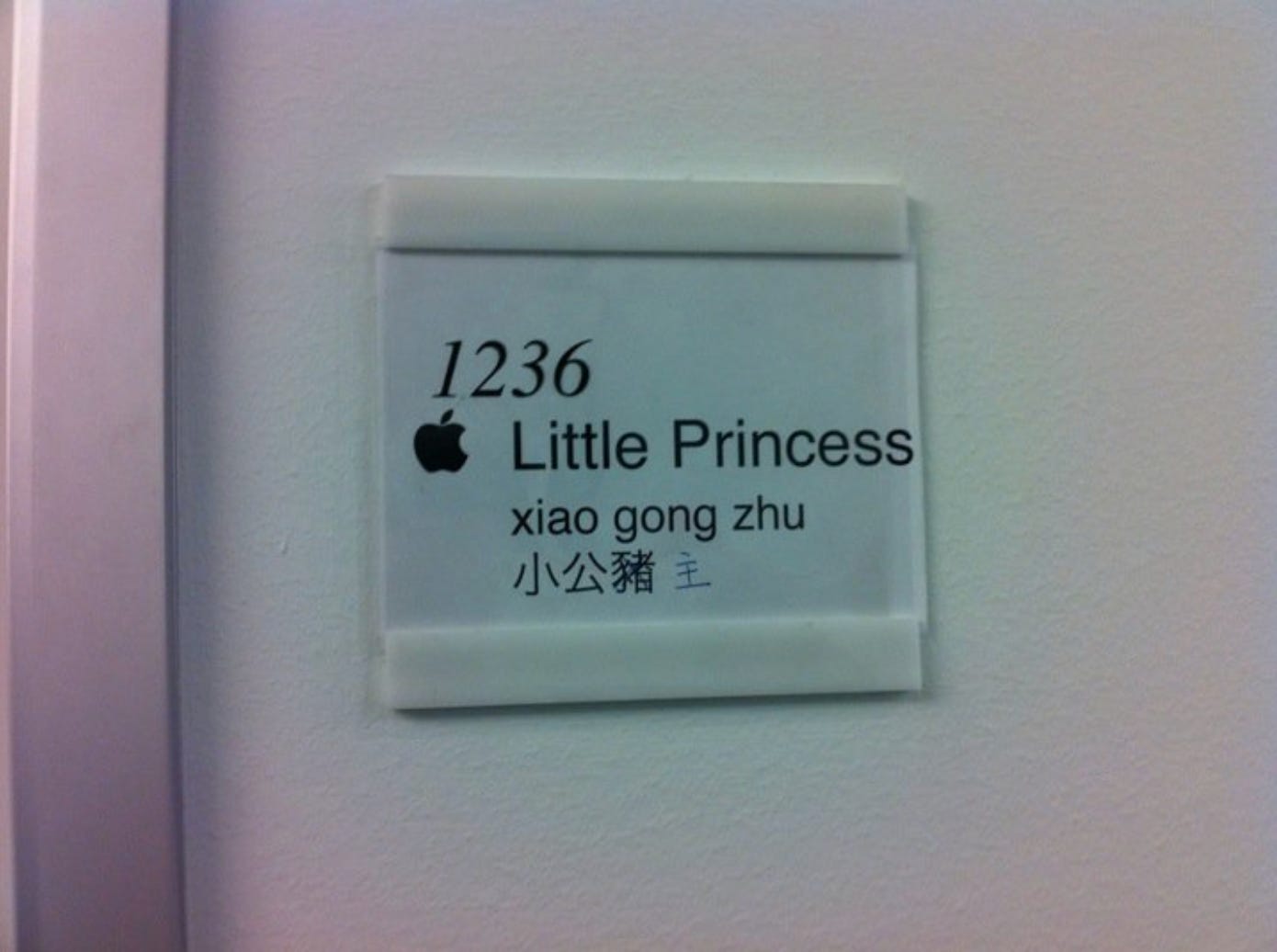
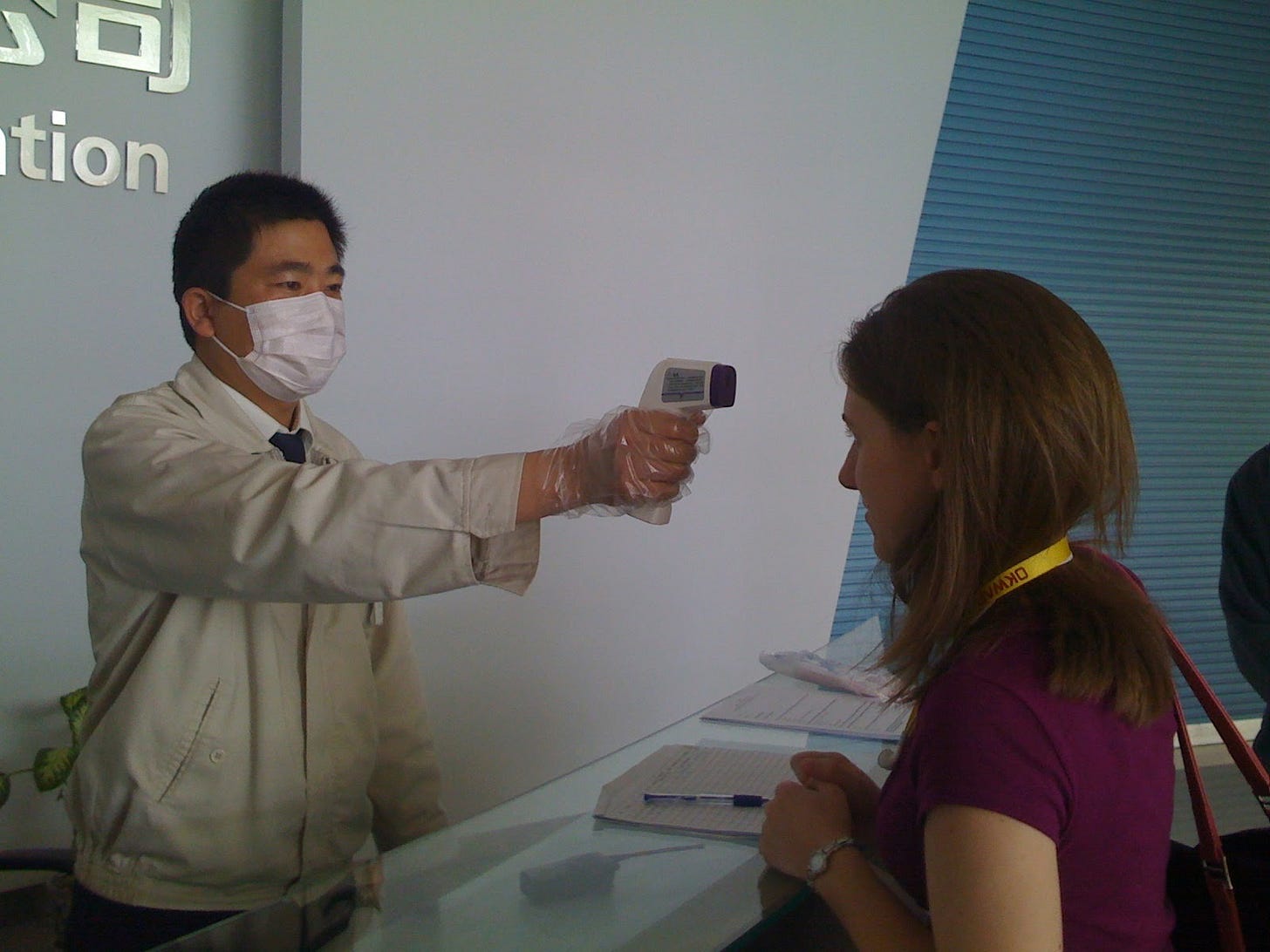
Another fun story: there was a time I was in China, and we were just starting to ramp up mass production on one of my product lines. This product had a microphone and we found a very very late breaking issue where the microphone would flat out stop working at certain cold temperature threshold. When we found this problem, we had already assembled tens of thousands of products ready to be boxed up and shipped. It was tricky: some microphones had this problem but some didnât, and we couldnât figure out why. We were already behind schedule and had to screenâwe had to find a way to get tens of thousands of units to low temps to screen.
Factories have thermal testing chambers, but theyâre pretty small, oven-sized. Any given factory only has a handful of them. In a moment of desperation, I ran to the factory cafeteria and emptied their ice cream freezer, and we tested our first product in the factory ice cream freezer. I turned to the sourcing person at the factory and said âcan you get me two dozen ice cream freezers by this time tomorrow?â I expected her to say no, but she looked at me deadpan and said âIâm on it.â The magic of manufacturing in Southern China is you can basically get anything any time. By noon the next day, a semi-truck completely filled with ice cream freezers rolled up and unloaded for us.
This is my favorite manufacturing miracle and the weirdest shit Iâve ever put on an expense report: dozens of commercial freezers.
What happened to the ice cream?
We ate a lot of Chinese ice cream sandwiches.
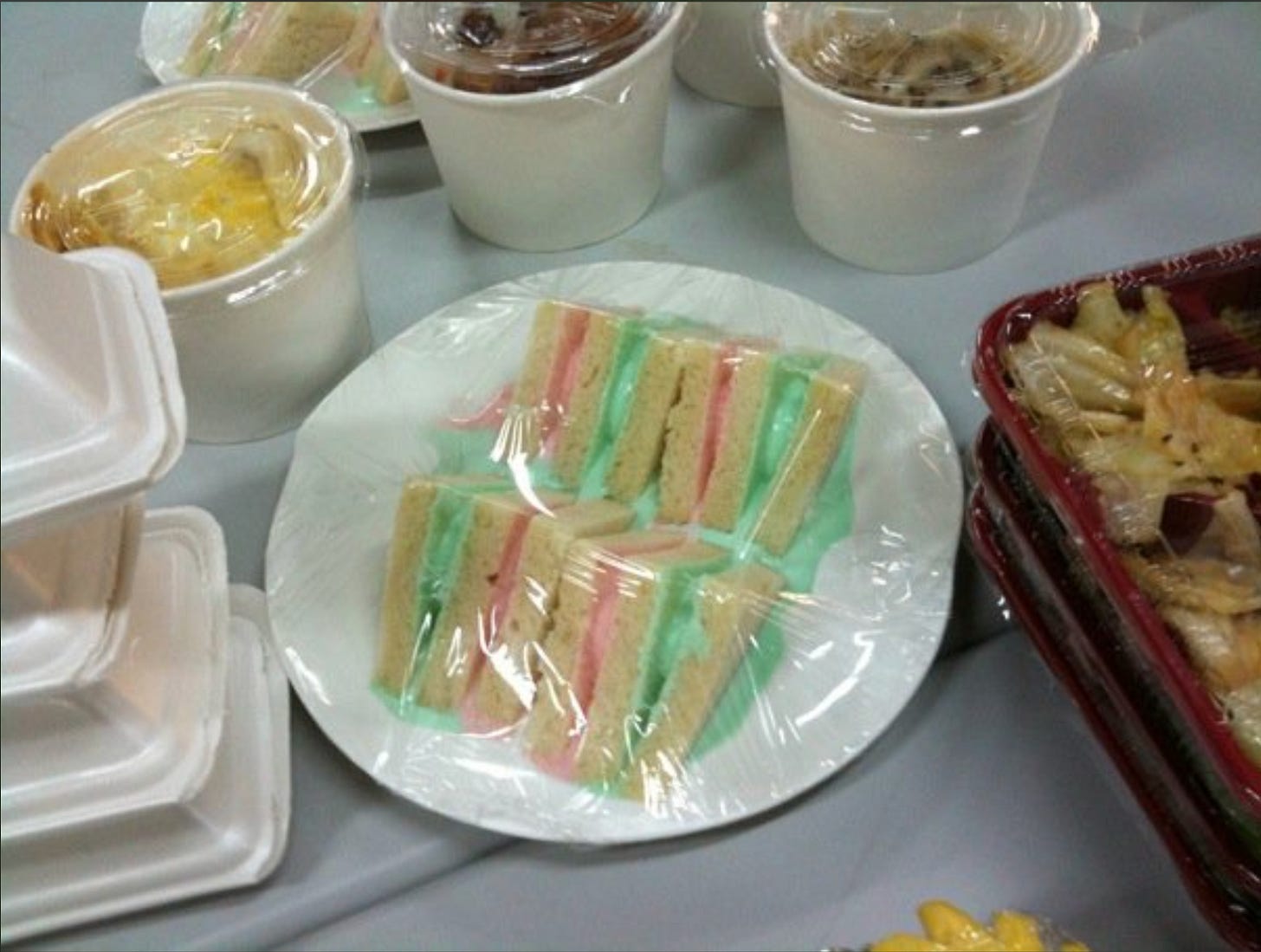
Iâve noticed you use hardware a few generations behind personally, whatâs the insider trick here?
I use software AND hardware a few generations behind. At Apple I always had to dogfood the nightly builds, so I constantly had a phone with weird bugs. Once the clock was counting backwards. I got so tired of it, now I just use something when I know itâs absolutely stable.
With hardware, I like new products, but youâll never find me waiting in line for a new generation of hardware. Thatâs because Iâve seen first hand in factories how crazy and chaotic the first few months of production are. If you wait a few months after a product is released, youâll probably have a better looking product: tolerances, offsets, etc will be better. Also possibly a more durable product: the manufacturer is more likely to have hammered out their processes.
You moved from iPod to Watch, a big shift for Apple. What are the big shifts in hardware engineering youâve experienced in the past decade?
iPod to Watch was a big shift in product, but from an engineering perspective, there was a ton of overlap. We used a lot of the same parts and suppliers. The first product designers (mechanical engineers) and system integrators (electrical engineers) for Watch came from the iPod team, including myself.
Over the past decade, the thing that wows me the most, is that when I started, if you wanted to build a custom circuit board, it took a minimum of four weeks and tens of thousands of dollars. Now I can go to Seeed, JLCPCB, PCBway, and I can get PCBs in a week for $50. It makes me so excited because itâs let everyone build electronics for fun. 3D printers get a lot of credit from the mechanical engineering side, but fast PCBs (printed circuit boards) have been a huge driver for hobbyists and new companies.
Why the drop in cost and time with PCBs?
I think manufacturers just figured out the processes better. And how to panelize designs with software so they could run a lot of designs at the same time.
Any cool projects youâre exploring now?
My toddler whoâs screaming as we speak, any time she misses her nap time, itâs catastrophic - the thing that Iâm trying to think through right now and next on my project list is putting electronics between my doorbell and crib camera. The doorbell chime makes my dogs bark which wakes up my kid. I want the crib camera to disable the doorbell chime when it detects sheâs in the crib.
If anyone has done something similar Iâd love to hear how they did it!
Whatâs your favorite simple (or not so simple) tool that you think is under-appreciated?
This oneâs easy: PSA! Pressure sensitive adhesivesâfancy lingo for double sided tape. I honestly think people would be shocked how many of their favorite products were held together by PSA. 3M makes good stuff.
If youâre working on or thinking about interesting hardware, hit me up at chrissy@root.vc â Iâd love to hear from you!
The Week in Review
August 9, 2020: 19th century Gothic hobnail safe by Magaud de Charf.
Iâm having a hard time tracking down more information on the manufacturer Magaud de Charf, besides that it appears in a few of the auction links for these safes. If anyone knows more, please let me know.
Manufacturer: Magaud de Charf (no link)

August 8, 2020: Rebalancing mountain goat populations with MD 500D helicopters flown by @utahdwr.
This is the same Department of Wildlife that restocks lake fish with airplanes! I honestly chose the wrong job.
Manufacturer: MD Helicopters
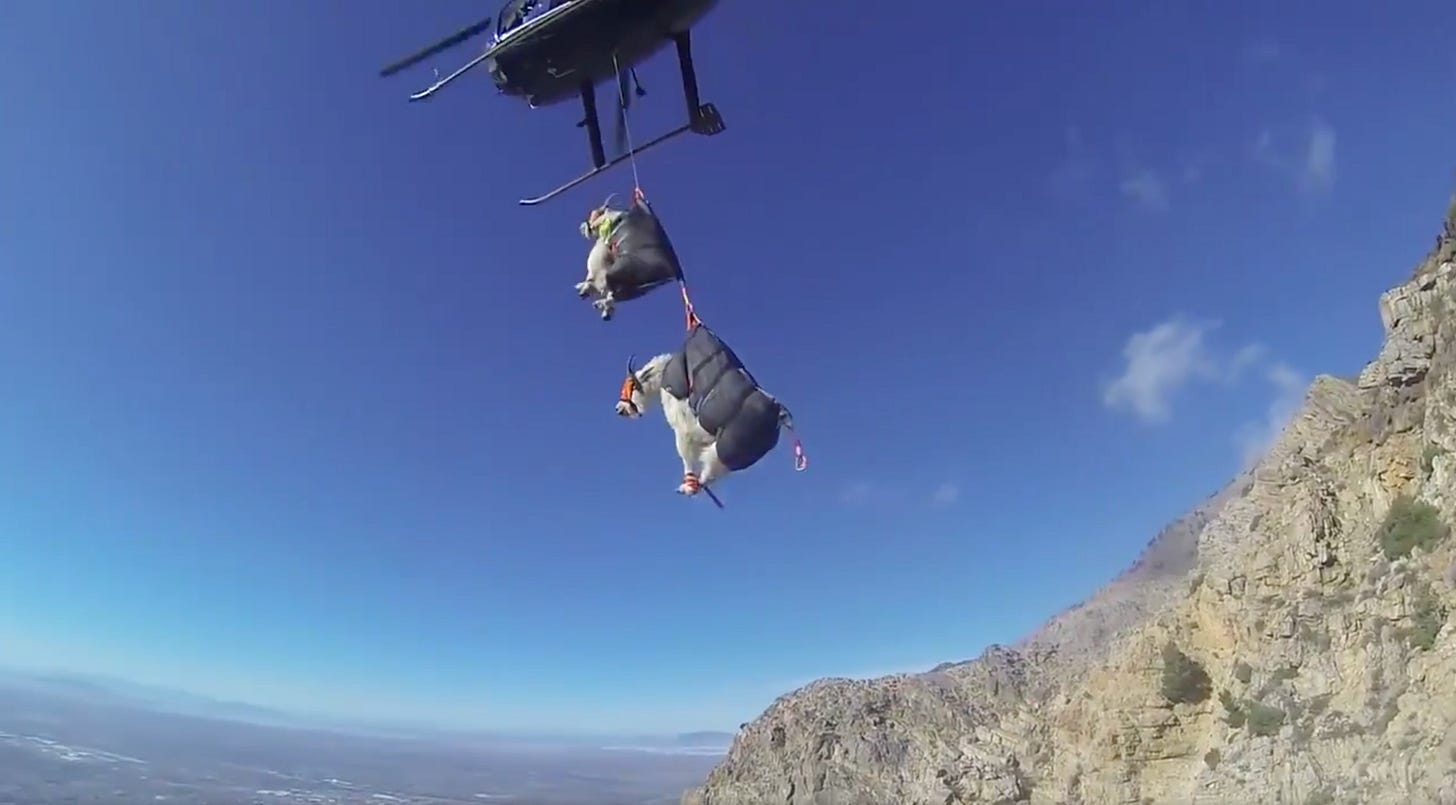
August 7, 2020: Loading 70mm film on an IMAX projector.
Film still has a je ne sais quoi - even the last Star Wars was partially shot on film. Film projection is much rarer though (film footage can be projected digitally), and seeing the size and complexity of this machine makes me appreciate why.
Manufacturer: IMAX
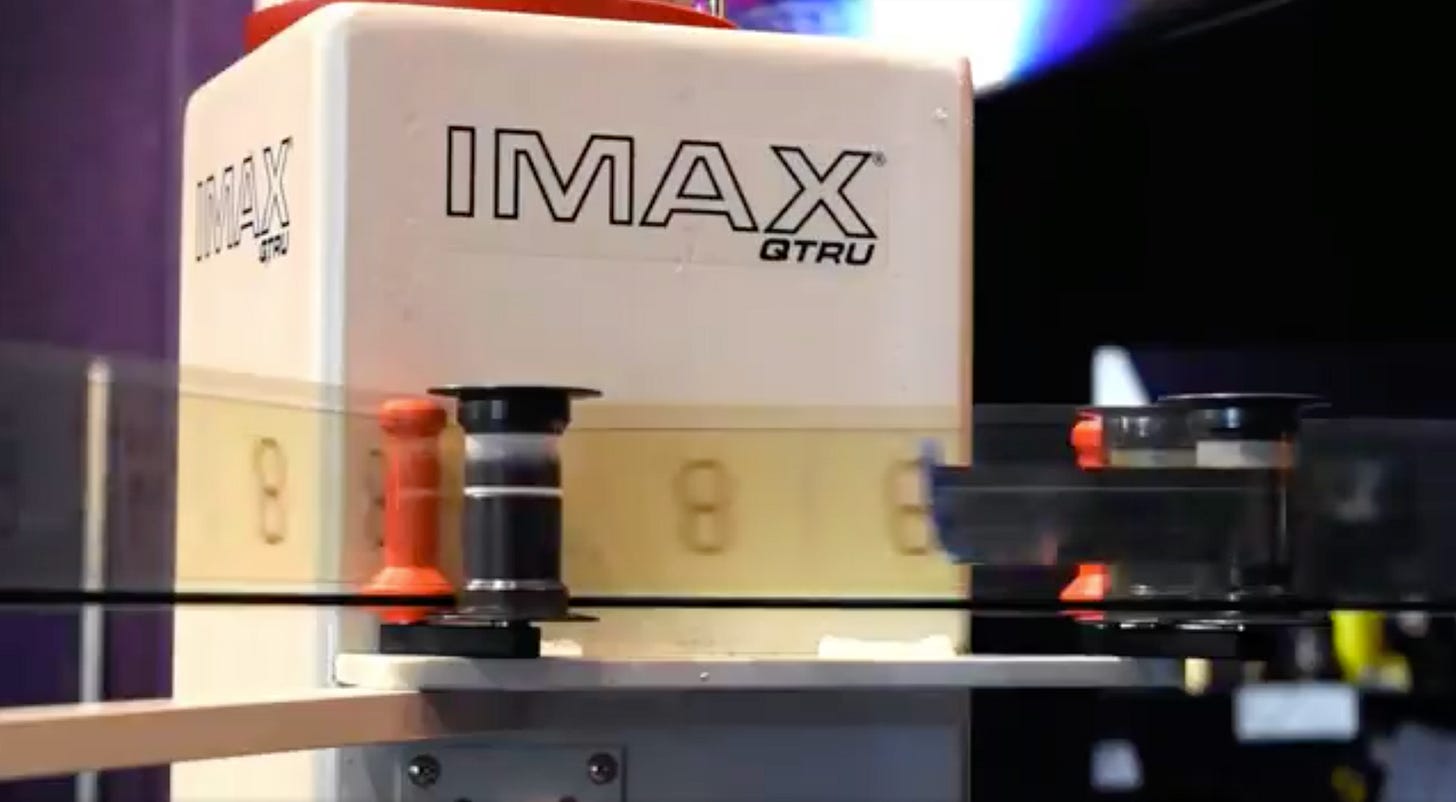
Postscript
This weekâs review is a little sparse because Iâve been Mad-Maxing across the Pacific Northwest with @quintendf and @jluan on carbureted vehicles. Thereâs something viscerally satisfying about a machine you can fully understand and fix with hand tools, with no electronic black boxes.
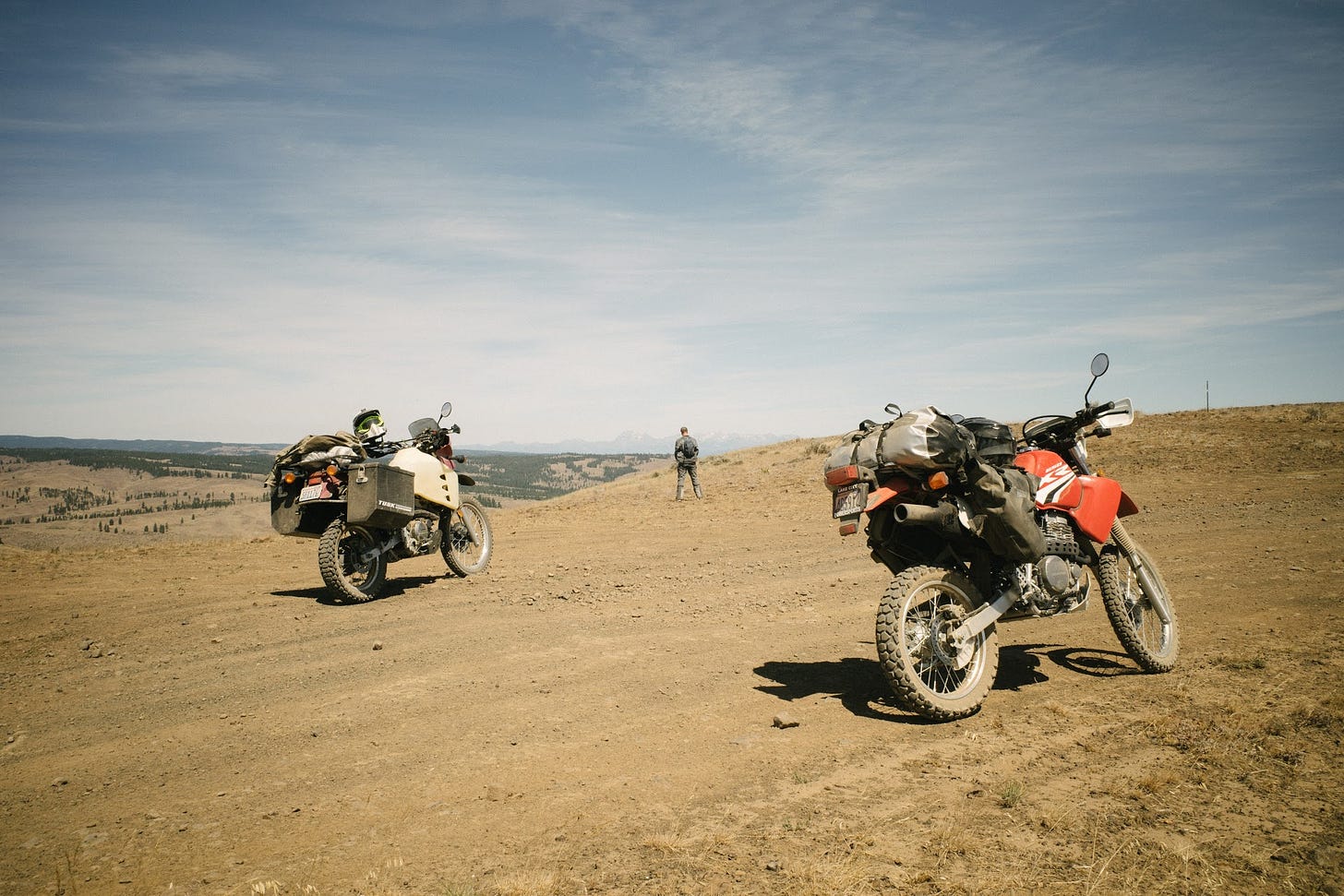
If you enjoyed this newsletter, forward it to friends (or interesting enemies). I am always looking to connect with interesting people and learn about interesting machinesâreach out!
- Kane