MachinePix Weekly #7: Mohit Bhoite, electronic sculptor
Freeform electronic sculpting with Mohit Bhoite. Also, a very popular train coupler 🚂
This week I sit down with Mohit Bhoite to talk about his whimsical freeform electronic sculptures. I met Mohit at his day job as Senior Hardware Engineer at Particle and have since been fascinated by his creative work which embraces old school analog design.
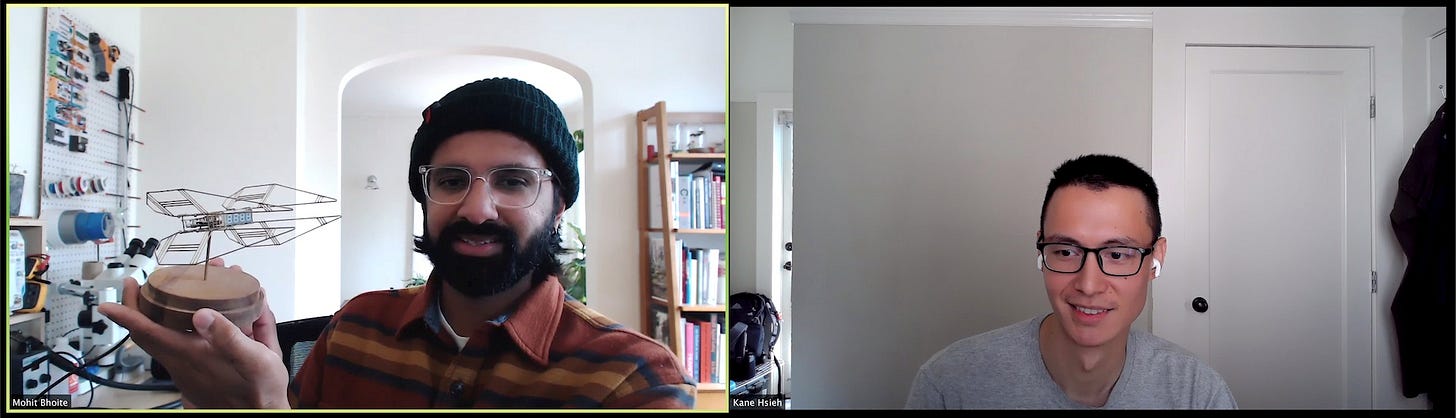
The most popular post last week was a Janney coupler between train cars. As always, the entire week’s breakdown is below the interview.
I’m always looking for interesting people to interview, have anyone in mind?
- Kane
Interview with Mohit Bhoite
How did you start making electronic sculptures?
Growing up I felt like I had three moms: my mom and two older sisters. One sister was art inclined, now an interior designer—the other was very good at math and became an economist. I felt like I was always between two worlds trying to appease both.
I wanted to build robots, and growing up in Mumbai, it was really hard to get parts. My sisters had a subscription to Reader's Digest in the 90s. I don’t remember the specific year, but I read an article about Mark Tilden, who was a researcher at Los Alamos National Laboratory. He came up with the idea of BEAM robotics, building simple robots with complex behaviors from broken tape players and very basic neural nets. He was using simple logic gates. It was amazing for me, I could just go to a scrap yard and get parts to build robots.
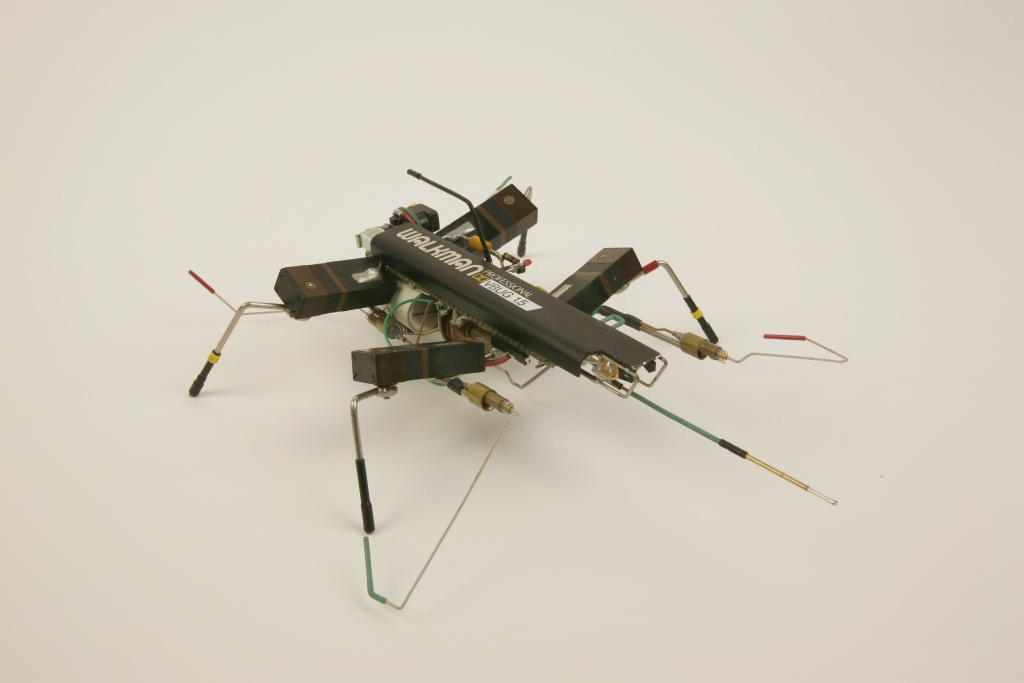
This introduced me to the “Dead Bug” method of building which does not require PCBs (printed circuit boards). The reason it’s called Dead Bug is because if you have an IC (integrated circuit) upside down with pins standing up for soldering, it looks like a dead bug. I’m not a huge fan of the phrase so I call it freeform electronics. I started building these as a teenager.
What was your first sculpture?
The first I remember I called it “Bumpy” in June 2000 - it was a 555 timer, two motors, and a relay. It would walk until it bumped into things and turn around. It’s not a sculpture per se, but the first project I remember getting excited about.
As far as sculptures go, as I recall, I was at an ACE Hardware in Minneapolis, and I came across a tiny display of brass, copper, and aluminum stock: sheets, bars, rods, etc. I saw a beautiful brass rod and I knew I wanted to do something with it. I ended up making a tiny fractal antenna for DirectTV.
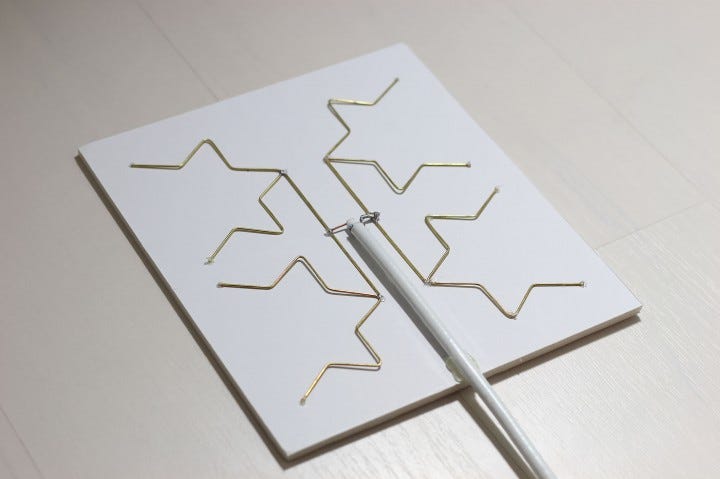
My first sculpture that got attention was SevenSeg. The reason I love love love seven segment displays so much is that they’re such a simple old school way of displaying information, but if you program it the right way it has a kind of face-like, anthropomorphic display. I can communicate simple expressions through it.
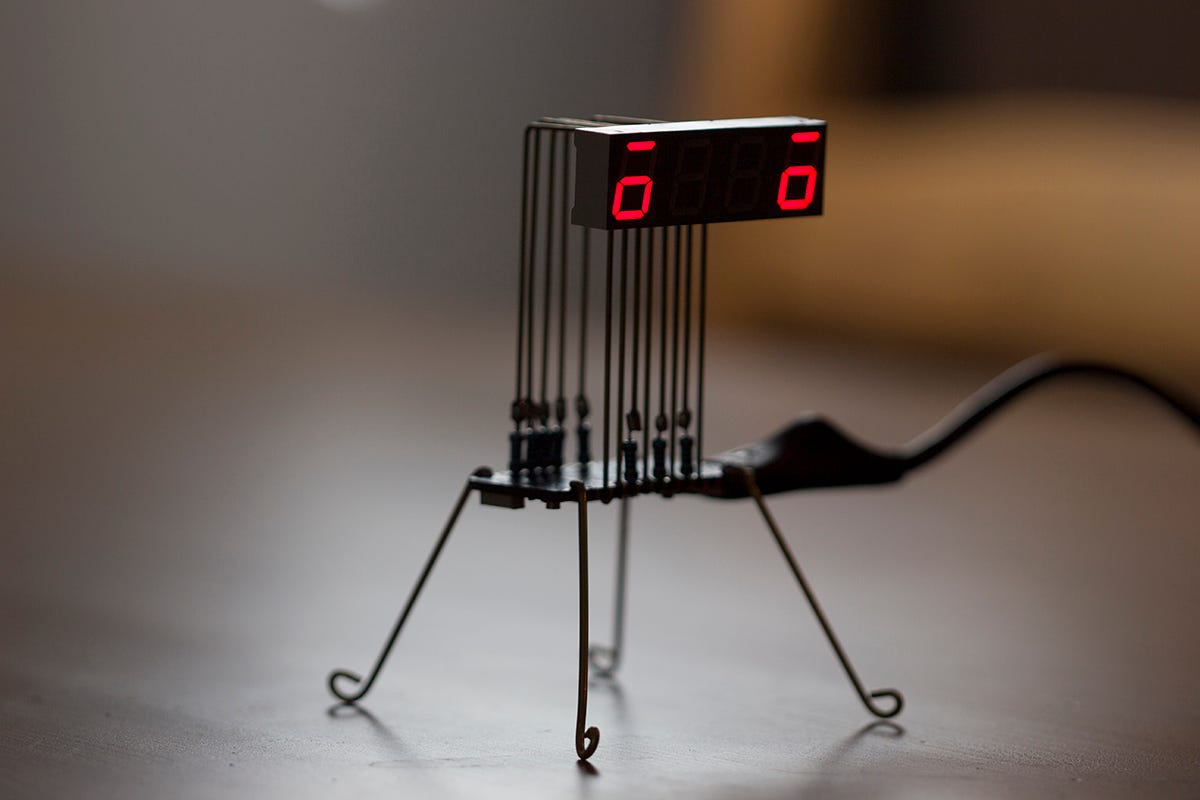
What’s the process like of designing a new sculpture? How do you draw inspiration?
A lot of Pinterest browsing! I’ve gravitated towards Japanese carpentry, and this seems bizarre, but there’s this instagram account that shows plumbing in a very clean spaced out way. Also my roots in robotics, and sci-fi with a lot of animatronics like Johnny Five and Star Wars where the robots are almost naked and you can see all of its movements. In my day job, PCBs are never the highlights, they’re always tucked away in an enclosure. I want to make electronics that are beautiful. I’m also fascinated by knolling and try to think about electronics like that.
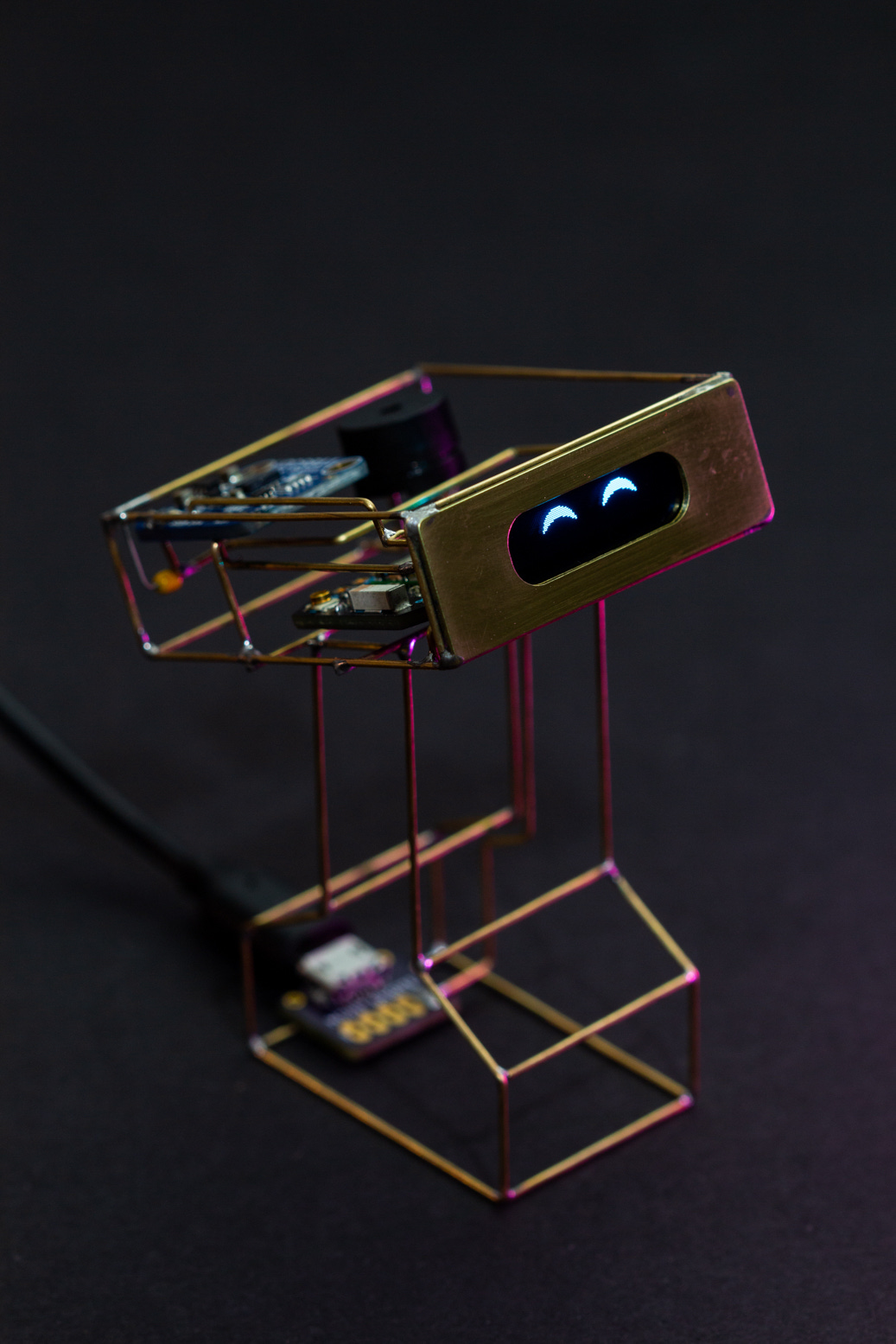
I bucket my sculptures into themes. If I let my ideas go free it’s really hard to pin anything down. Some I’ve used are “Handle with Care”, where I had six wooden handles and I wanted to do something with them, “Satellites and Spaceships”, and “Seven Segments”. That helps me start.

What is the process? Do you have it fully planned out before you start?
A lot of doodles! I draw a lot of loosely thought-out ideas, and then go about thinking how I would build a sculpture around it. The latest one I’m working on is a tiny FM radio. I just start doodling, and when I draw something I like, I make a template in Adobe Illustrator for the form. I’ll use Autodesk Eagle to draw the circuits, but with brass rods in mind, not PCBs. Eagle only allows you to design in 2D though, so I’ll do multiple layers to make a 2.5D design which I start sculpting around.
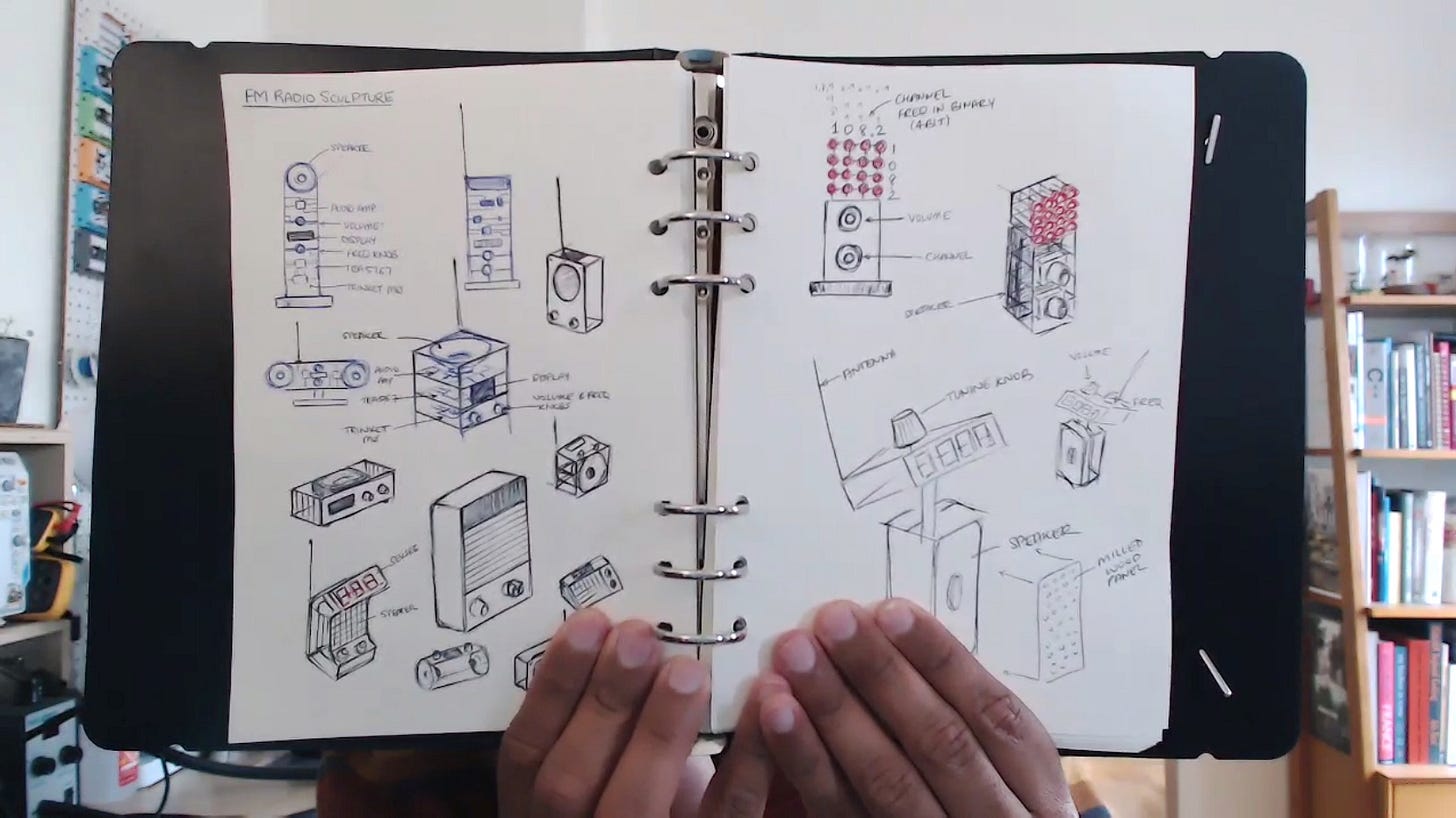
Before I solder I’ll breadboard the project to prove it works. When I start sculpting, I can still improvise, because I’m working in 3D space.
What is the hardest part of creating these sculptures?
Oh man, it’s the engineer in me that’s my biggest enemy. When I’m building sculpting as an art form, the engineer inside me is always asking why I’m doing this. These are solved problems. Why go through this convoluted process? Trying to appease the artist and engineer is challenging and sometimes I lose motivation. There was a sculpture I was trying to make as a 3D matrix of LEDs. It was extremely painful, It would have been so easy on a PCB, but I wanted to explore what would happen if I didn't have a PCB!
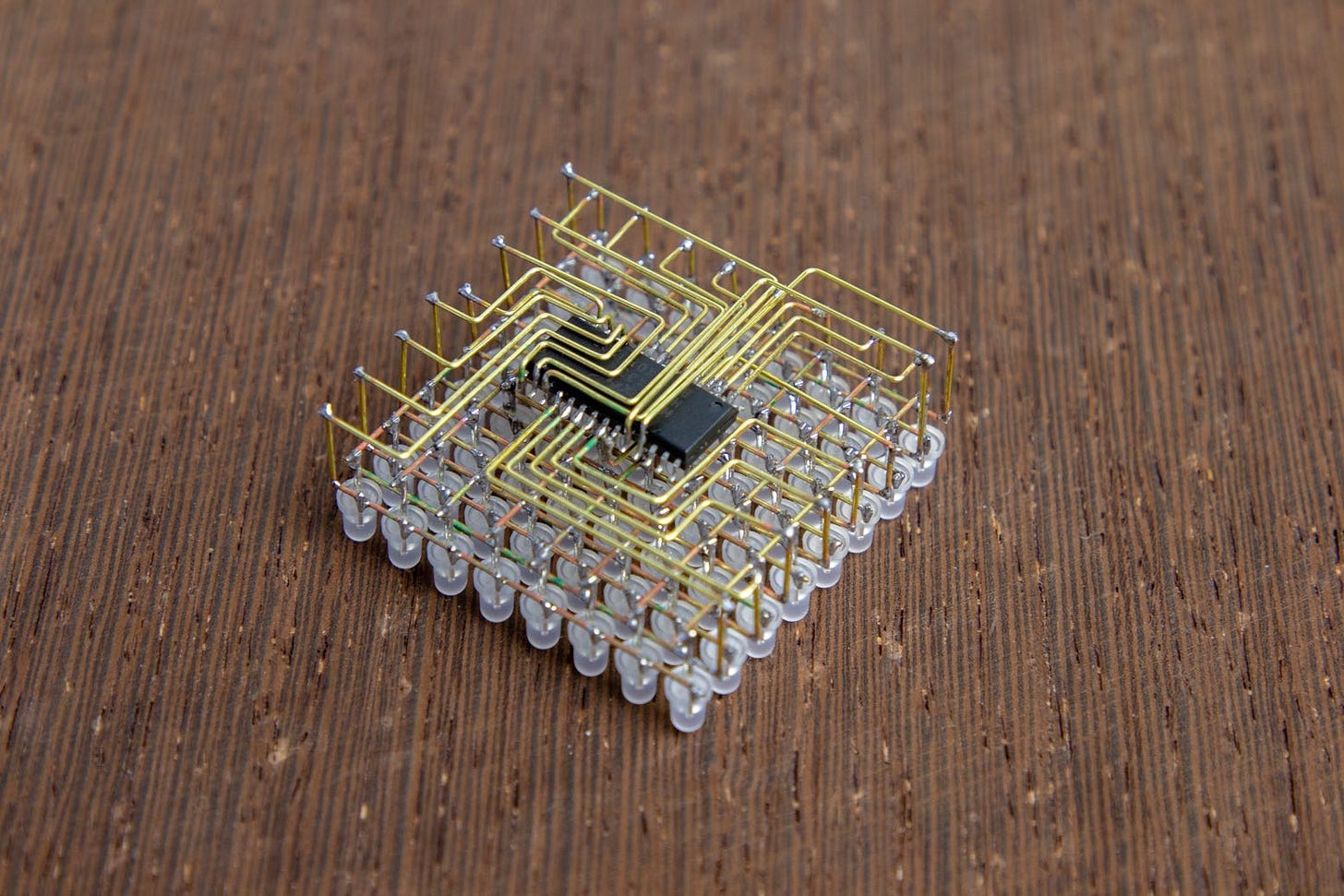
How do you overcome those blocks?
Since I have a day job, I can't sculpt for long stretches. So I just walk away and think about something else. When I come back a day or two later, I’m in higher spirits. Also making sure I’m well-fed. Everything is worse when you’re hangry.
What’s your favorite sculpture you’ve created?
I have a couple, but the reason I’m choosing Xenyan is that it combined my passion for robotics. Xenyan isn’t a static sculpture—it can be programmed to drive around and paint with light for long exposure photographs.
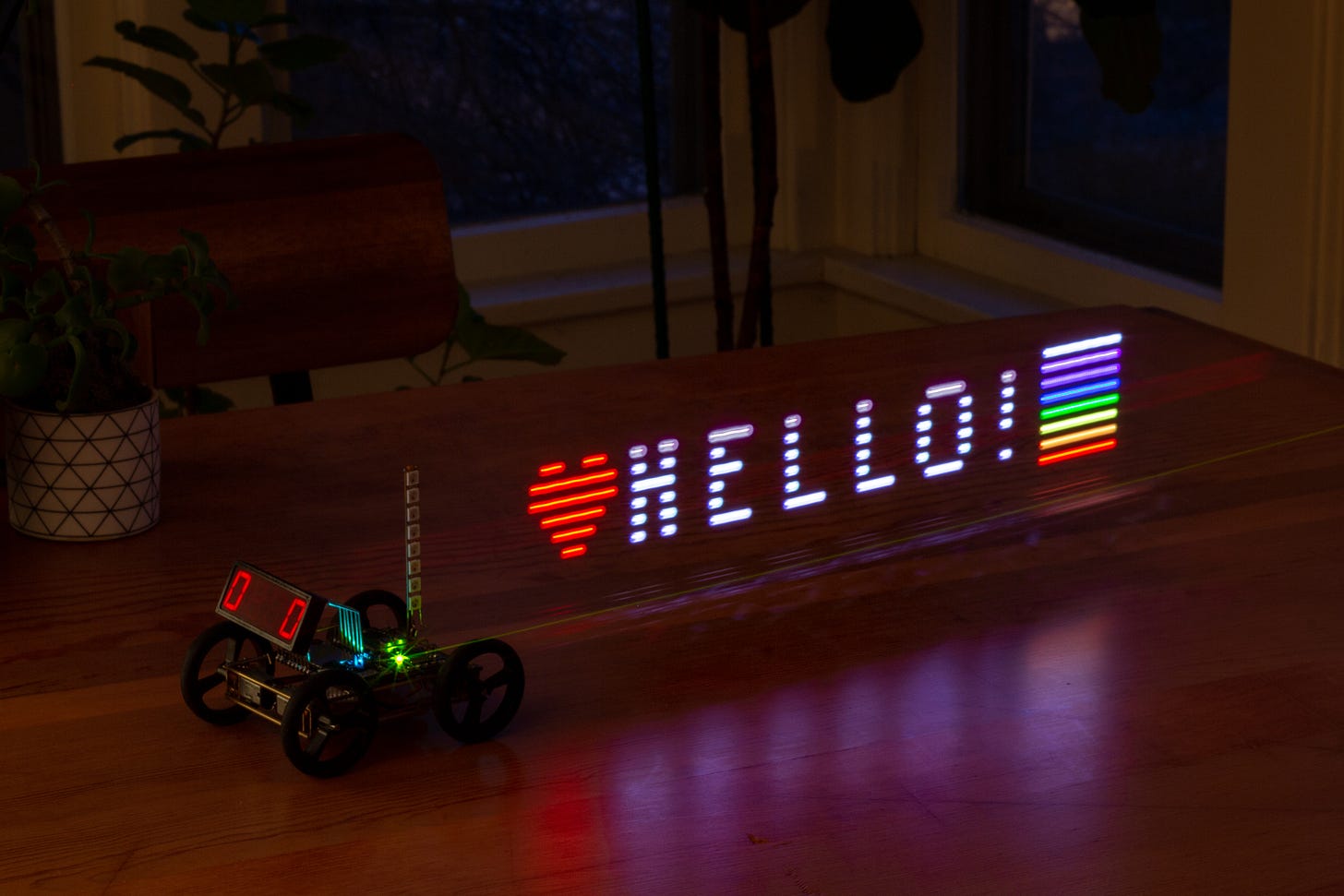
My second favorite is Chintoo because it let me combine multiple media. I used milled brass, wood, and a seven segment. I would love to work with ceramics in the future. Also nixie tubes.
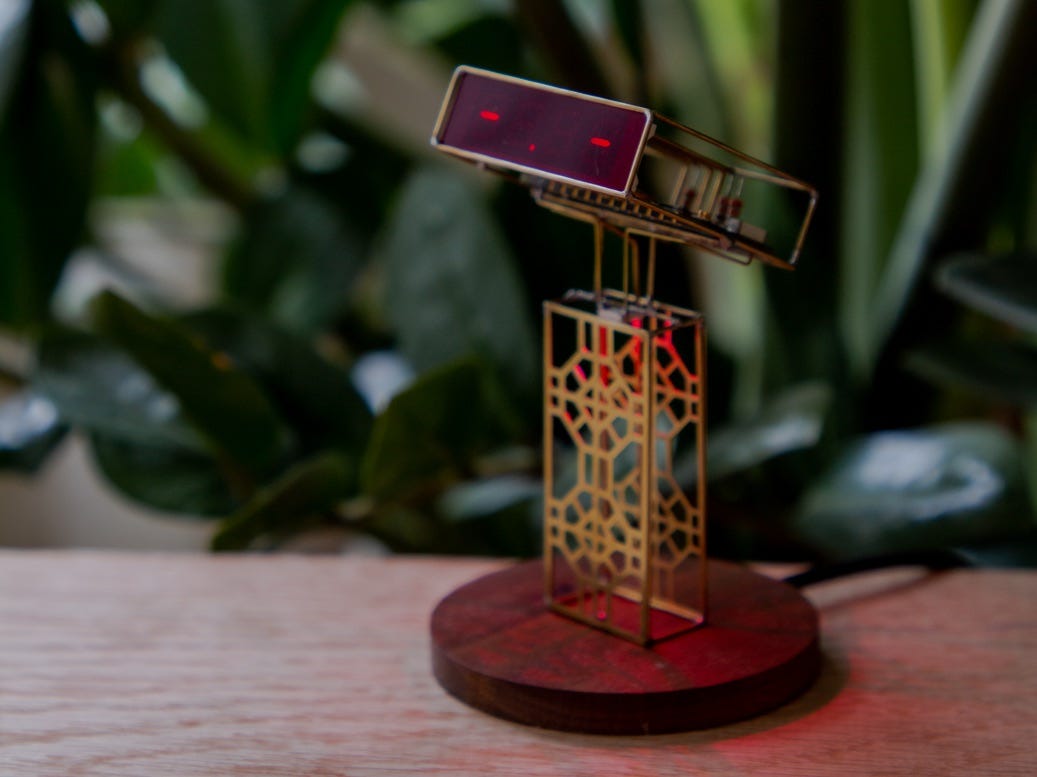
Who else is doing interesting creative work around electronics?
Greg Davill I started following recently. He makes building circuit boards look really really cool. The way he photographs and applies the solder paste, it’s amazing. He’s making FPGAs, thermal cameras, all kinds of stuff. Just a fun account to follow.
Jiri Praus, I think he started making sculptures with brass. He made this tulip on Valentines Day that blooms. His work is very ornamental; my work is a lot of straight lines and hard edges, his are very organic. Seeing more people involved in this kind of work is inspiring.
Any cool side projects you’re exploring now?
I’m trying to reignite my love for ham radio and satellite communications. It’s amazing what you can do with a 5 watt radio. I want to make antennas. Now you can combine SDRs (software defined radios) and get images from NOAA weather satellites, it would be fun to have a live image of the San Francisco fog.
On Instagram, kids are reaching out asking how they can learn more or get a job around their hobby or work on robotics when they don’t have a lot of tools. When I was 16, I sent an email to the owner Solarbotics asking how I could get into robotics even though I didn’t have access to materials or courses. He told me to take electronics courses and learn CS on the side. It changed my life. I always try to respond to kids now, it’s a way to give back to the community.
What’s your favorite simple (or not so simple) tool that you think is under-appreciated?
The Xuron 9100F flush cutter with a retainer clip. There are so many tools I like. Before I was using this flush cutter, when I was using cutters without retainers, every time I made a cut, some piece would go flying. In a carpeted apartment it’s a nightmare. It’s such a simple thing, but now it’s the most heavily used tool in my toolkit. A life changer.
The Week in Review
These lil tugs are used to move ships around and deploy underwater fences. Colloquially called Boomin Beavers, their rotund hulls are visible by satellite at a few Naval bases.
Like all hobbies, keyboards are a rabbit hole deeper than you could possibly imagine. Recent keyboards with hot-swappable switches mean we are in a golden era of keyboard switches. I am partial to my Vortex Race 3 with MX Blue switches but I am sure many of you will tell me why I am wrong.
I learned that it’s common for roofs to have rock ballast to protect from UV and precipitation. So of course rock vacuums exist.
This week’s most popular post! According to a Twitter follower, these couplers are proof loaded to 900,000 lbf. Wild.
This solicited a lot of “but whys”. It’s smoother and vibrates less than a jigsaw. Also, it’s awesome. That’s why. Sadly, not available in the US yet ☹️
Postscript
I’ve been learning to use my Brother PE800 CNC embroidery machine. Automatic bobbin winding and needle threading are incredible. These may be common features now, but the sewing machine I learned on as a child did not have them and I spent a lot of time cursing at needles. I look forward to tripping down the embroidery rabbit hole 🧵🌚
If you enjoyed this newsletter, forward it to friends (or interesting enemies). I am always looking to connect with interesting people and learn about interesting machines—reach out!
- Kane