MachinePix Weekly #36: Milo Werner, former Head of New Product Introduction, Tesla
Milo Werner talks about the challenges of shipping the Tesla Model S and X and what the Next Big Thing is. This week's most popular post was a cute personal train đ
This weekâs interview features Milo Werner, the woman who ran New Product Introduction (NPI) for Tesla and launched the Model S and Model X. If youâre new to NPI, check out this excellent definitive guide. If youâve already been in the trenches, or are just here for the storyâREAD ON.
The most popular post this week was these cute little trains between the Halligen islands in Germany. Thereâs a German public broadcast show on these trains, which YouTube will auto-translate subtitles for!
Iâm always looking for interesting people to interview, have anyone in mind?
âKane
Interview with Milo Werner
You started your career in civil and environmental engineering. What brought you into the world of EVs?
I spent three years as a geotechnical engineer, and the work was very prescriptive. Most engineering work is, or was, done with catalogs and books. Measure the strength of the soil and then reference a table in the ICC to determine the footing size and reinforcement. It just felt very mundane.Â
The advancement in processing power made Finite Element Analysis much more accessible and changed the industry to be a lot more interesting. In the early 2000s, we had those tools but there was one computer in the office dedicated to modeling and it took 12-24 hours for a single run; One engineer in an office of fifty did all the modeling. It was very much not actively used.
I went to the MIT Leaders for Global Operations program where you receive a Masterâs in Engineering and an MBA. A core part of the program is a six month internship at a sponsorâs facility writing an operations-focused thesis. I wrote mine at Intel on the impacts of unplanned equipment downtime and reentrant process flow. There wasnât a lot of creativity offered and it felt like the same path I was on as a civil engineer. A âcopy exactlyâ climate was not what I was looking for.
At that time, Tesla was taking preorders for the Roadster, and I had a friend who bought the first one. I thought it sounded really cool; and during the month of January, I decided I would try to work at Tesla. I asked everybody that I knew, including the friend who had bought the Roadster, who gave me Elonâs email address. I emailed him directly, he didnât respond. I emailed a lot of other people and finally someone responded, and I started January 2, 2007 for what would become an amazing eight year journey.
I remember the first generation Roadster! Itâs awesome but Iâm lanky and the one time I got to try it it felt a bit like a clown car.
It does feel a little bit like a clown car. I was eight months pregnant when we had two prototypes, and I had to get onto my hands and knees to get into the car.
Thereâs a surge of mandates and OEM adoption now. When you started at Tesla in 2007, it was much harder to say EVs were a forgone conclusion. What convinced you, and what were the toughest parts of working on EVs then?
Well, when you don't have any comparable experience, it feels like a rocket ship; youâre a lot more patient to wait it out. Itâs not like I was coming from Amazon or Google or any of those super successful companies, right? I was coming from civil engineering, which felt like a dead end, so I was much, much more patient about waiting for the adoption. We were still in the land of the Who Killed the Electric Car? movie; that was still what most people wanted to talk about when I said I worked at an EV company.
Stepping back, it felt there was nothing better out there to work on, so who cared if it took ten years? There was no place else to go that could be more important.
What are some things that people may not realize or appreciate about shipping EVs, especially compared to ICE?
One, EVs have very few moving parts. The cost of maintenance on EVs is dramatically less, which is why the cost of ownership is so different for electric cars.
Theyâre also much more modular than a traditional internal combustion engine (ICE) vehicle. When you import a car into Europe, you can avoid the import tariff by assembling half of the value of the vehicle in the EU. For an ICE vehicle, think about assembling the engine and transmission: getting to that dollar value is really difficult. In an EV, the dollar value of the motor and battery is about 40â50% the price of the car. So the way Tesla imported vehicles into Europe in 2015 was to install the battery and motor in the receiving country. Itâs a few dozen bolts to install the battery and drive unit.
I recently switched to an EV Zero and I donât miss the gas engine or shifting at all.
For a long time, I drove a biodiesel VW Golf. Moving from a Golf to a Model S was like night and day; I'll never go back.
As you look to the future, what opportunities will EVs unlock for us?
One of the biggest opportunities that I see on the horizon is the integration of vehicles to grid and home. A lot of people are installing batteries in their homesâbut in the US, the energy consumption of a home is so much greater than what a home battery can provide. The home battery is not a viable backup solution. Even if batteries were free, the solar power installed on a standard US residential roof cannot charge a battery that would support your home for 24 hours. Eight-plus hours maybe, but itâs just not possible for 24 hours.
If youâre driving around a 100kWh battery, thatâs going to support your home for up to three days. Itâs a huge, huge battery. I actually think that home-installed batteries will be primarily used for peak shaving afternoon-evening demand. For true backup power, weâre going to install energy management systems with prioritized load capability similar to Span.io that will leverage the vehicle battery and rooftop solar and power the home for days. I can see a place where small generators, maybe natural gas or fuel cells, will play a part in the near futureâbut I just donât see mass adoption of home batteries in true full off-grid applications.
Is that limited by the chemistry or engineering and process?
I think it's a combination of how the technology is advancing and the speed of EV adoption. The people who are buying home batteries are the same group buying EVs. I do see combined batteries and rooftop solar getting to the density and size where they can power your home for days. But the speed of adoption of EVs will overtake that and it will make more financial sense to do vehicle-to-grid or vehicle-to-home support than it will to buy a large expensive home battery. Youâd own two of the same thing!
Even now, the Tesla battery for home isnât that big: 14kWh. People may buy one for redundancy, but you have to buy two or three for multi-day battery backup. The price for a single Tesla Powerwall with associated hardware is $8K, uninstalled. Thinking that people are going to pay $16K to $24K for home backup power they will use once a year, when you already have that battery in a car, seems like a stretch.
What are the craziest stories youâre able to share from your experiences?
There definitely are some crazy stories. One of the pieces that I always advise companies on is balancing how much theyâre willing to pay to accelerate a product launch. The craziest stories for Tesla are when you shut down a 5,000-person factory for seven days, totally unforecasted. Itâs a huge expense. Thatâs when you do cartwheels to make things happen.
Running New Product Introductionâitâs not unheard of for those problems to occur with the product I was in charge of. Maybe people order the wrong parts, or parts we thought would work actually don't. The real cost of bringing the factory down isnât just the paying the direct labor to stay home; itâs also the cost of making a 1,000-person engineering team wait for the operation to catch up. Thatâs millions and millions of dollars. Then you start thinking, âHow can I get this part in to keep the schedule?â Now weâre talking about chartering flights, chartering 747s to bring parts in.
Did you have to charter a 747?
Tesla has chartered 747s, back in the day, for sure. When you think about the cost of chartering a flight versus the cost of production and engineering downtime, itâs much more effective to just get the parts. The cost of a delayed product launch is not just the missed revenue, but also the cost of carrying the 1,000-person engineering organization and delaying them from working on the next product. When you realize this, expediting prototype and production materials takes on a whole new meaning, and Tesla could justify paying crazy expediting air freight fees and, in some cases, chartering 747 cargo carriers.
My colleague Chrissy worked on NPI for Apple, and wanted to know the craziest reason you had to stop a line!
When we were launching Driver Assist, now called Autopilot, we rebuilt the low voltage vehicle electronics and most of the facia to accommodate sonar in the bumpers, radar in the grille, and forward cameras in the windshield mirror assembly. At the same time, someone decided to slightly change the windshield shape; I don't remember why. The repercussion of it was that the forward cameras could not calibrate because there was an internal reflection within the windshield. The infrared layer was causing a reflection not seen in the original windshield shape. That was an instance where we air-shipped three weeksâ worth of old windshields from South America while we dealt with that situation. You can imagine that was an exciting time. Elon was at the factory daily, and design engineers were taking shifts calibrating every vehicle around the clock.
How has the NPI role evolved since the Roadster?
The Roadster operated in a kind of Big Bang, where we just had to get a product to market. It was the only product we had, so everyone was working on just that one product. It was clear the Roadster was not a car that appealed to a huge population, so we quickly developed the Model S, and the Model S NPI is built on an iterative modelâstill at Tesla today, NPI is a continuous integration.
When we launched the Model S in 2012, the powertrain was based on a Toyota RAV4 powertrain Tesla designed in 2011, and the chassis and body were all new. Then the Model S had integrations through its life including autopilot, performance plus, dual motor all wheel drive (AWD) and many cost-down programs. It was common for the NPI team to be managing 50 part changes every month. The entire motivation behind dual motor, Teslaâs AWD, was to mature the Model S powertrain in preparation for Model X, an SUV which would of course have to offer AWD. When Model X launched, it was built on the powertrain of the Model S with a new taller body. Within the first year of production, the Model X chassis was redesigned to be the same as Model S. Unlike the Roadster, which was the Big Bang, âhere it isâ moment, the S and X are iterations upon iterations.
Whatâs the relationship like between the design, NPI, and production groups at Tesla?
Super integrated! The teams start at the same time and work together right from the beginning. Historically when you talk to product developers, thereâs a reference to âthe Wall,â where engineering does their work and they throw it over the wall to operations and production. But at Tesla, it all happens together from the beginning.
What are the tradeoffs of that engineering culture?
The positive is that it shortens the launch times. You're not waiting to pick manufacturing equipment when you get to a mature design; youâre able to pull that timeframe in. The negative is that sometimes you have to make decisions that lock you in earlier than you would like, because you are developing the assembly and automation in advance. Thatâs what leads to continuous iteration: you make some sacrifices to get to production quicker, but as you have time to step back and look at the whole engineering and manufacturing design, there may be more changes you want to make.
Whatâs your favorite vehicle youâve worked on?
At home I have a Model S with many, many miles and an uncountable number of prototype parts. Thatâs my favorite. My car along with many other employee cars were used to validate pre-production assemblies. Iâve had multiple dash assemblies, center console screens, and countless seat configurations. Every time my car needs a repair, itâs an ordeal because the parts donât match the as built documentation. For instance, the threads that held my driver seat to the frame were stripped because weâd tried so many seats, so finding a replacement that worked took like nine months.
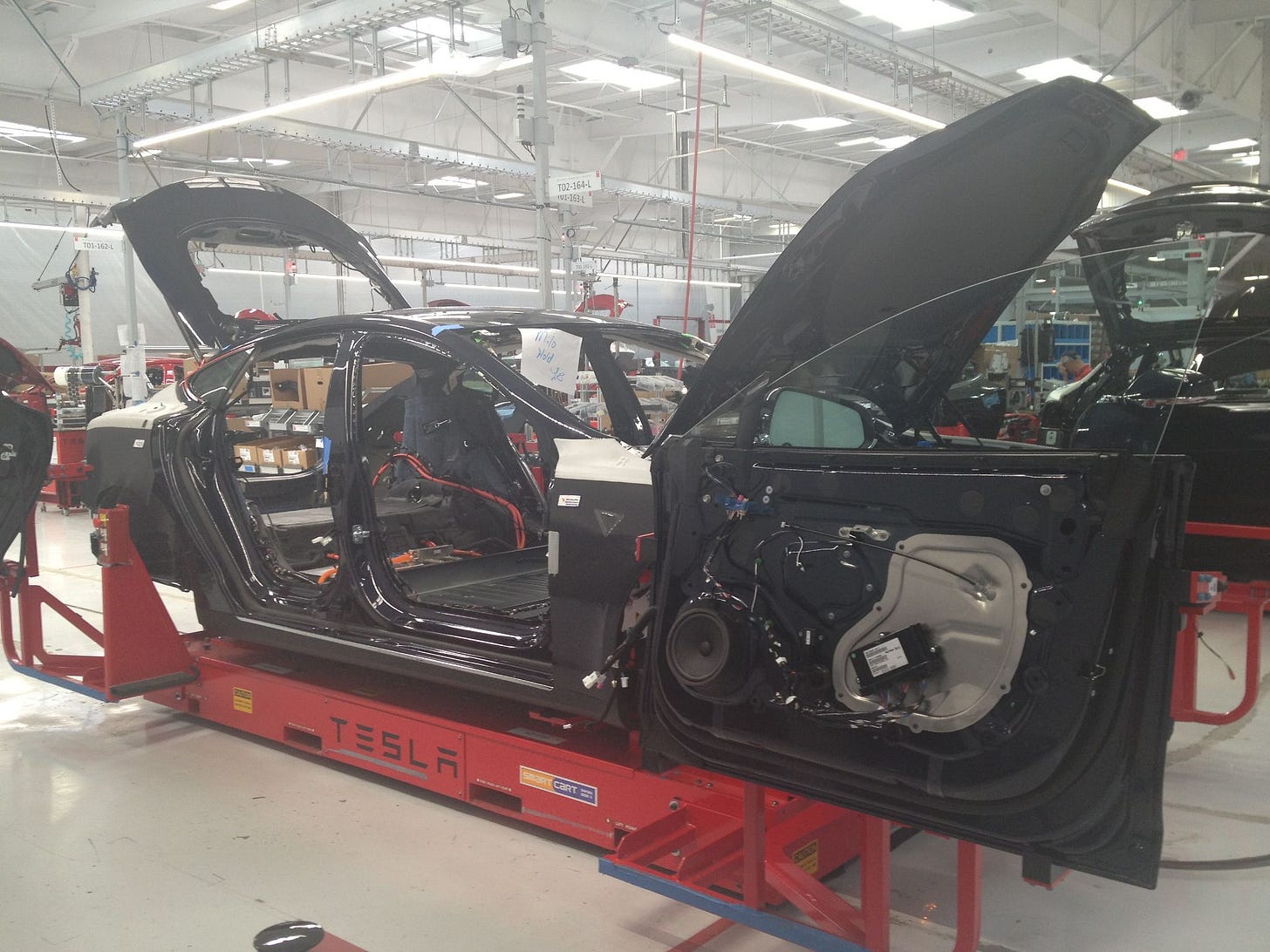
What are the things that you have conviction around now that people are missing, in the same way Tesla was ahead of the trend in 2007?
Yeah, I think that weâre just starting to crack the nut on air quality monitoring and building energy management. COVID has really brought this to the forefront of everybodyâs vision. Iâd also say that Californians are experiencing itâclimate change, wildfiresâin a much more severe way, which is making us deal with it.
In 2018, the entire west coast had such bad wildfires that many schools shut down and they couldnât reopen until HEPA filters were installed. This past fall, because of COVID regulations, schools couldnât close the windows and without HEPA filtration, the schools were again closed for numerous days during wildfire season. This year is anticipated to be more of the same. Students will not be vaccinated and wildfire season is expected to be severe with much of the state having received less than 50% of the average rainfall. These are indicators that weâre going to have to get much better at managing indoor air quality. There are some things that are happening outside, like Purple Air, that people in California are watching obsessively. Indoor air should take on a similar level of concern. VOCs, CO2, particulatesâright now people just run HVAC to cycle the air, but thatâs insanely expensive and energy intensive. Monitoring, modeling and systems optimization will be key in the future.
What is Ajax and what do you spend most of your time on now?
Yeah, Ajax is a venture fund dedicated completely to investing in entrepreneurs solving climate change. We believe we have 98% of the technology to solve climate change; now itâs just industrializing it. Itâs a very tactical fund. We have most of what we need; we just need to industrialize.
Are you working on any side projects these days?
Iâve pretty much committed my life to climate technology, if weâre going to be completely transparent. I want to hike more; that may sound a little lame. I would love to spend more time outdoors.
Any favorite books or books youâre reading right now?
Yeah, I love Radical Candorâprobably my favorite book.
Whatâs your favorite simple (or not so simple) tool or hack that you think is under-appreciated?
I was reading that question this morning and didnât have a chance to think about it. I donât feel like this is under-appreciated, but I feel like taking real-time notes in Google Docs is so under-appreciated. Some people are taking handwritten notes and I donât know why.
The Week in Review
Fun fact: thereâs always at least one Soyuz docked to the ISS as an escape craft.
Despite the unavoidable comparison to the turbo encabulator, turbulators are real things.
The C-5 is the largest aircraft operated by the USA, which is still smaller than the massive AN-124 flown by Russia, both of which are smaller than the gargantuan Scaled Composites Stratolaunch.
Itâs funny and a little bit romantic to think that bubble wrap sends you a little bit of the air from where it was packed!
Postscript
I was inspired by Kyle Wiensâs and Laura Kampfâs work with scrap material, so my housemate and I visited a junkyard to scavenge some ICE parts. I wonder what EV junkyards will be likeâthey are inherently more solid state than ICE and will have more challenges with interoperability.
If you enjoyed this newsletter, forward it to friends (or interesting enemies). I am always looking to connect with interesting people and learn about interesting machinesâreach out.
âKane